製品開発において複雑な形状や高精度を求める試作の部品では、試作コストが予想以上に膨らみやすくなります。これにより、「金型費用が高すぎて予算オーバーしてしまった」「試作の回数を重ねるごとに開発費が膨らんでいく」このような悩みを抱えていないでしょうか。
本記事では、試作にかかるコストを削減するための具体的なアイデアと方法を紹介します。開発予算内で質の高い試作を実現するためのヒントを見つける参考にしてください。
試作のコストダウンが重要な5つの理由
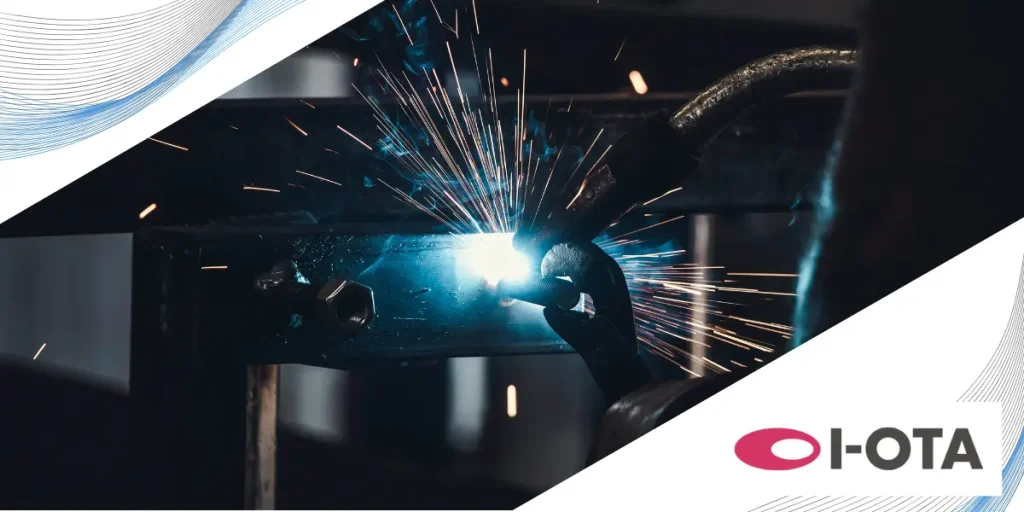
試作のコストダウンが重要な理由は、以下の5つです。いずれにおいても、単に「お金を節約する」以上の意味を持っています。
- 予算を最大限に活用するため
- 市場投入までの時間を短縮するため
- 競争力を強化するため
- 量産時のコスト予測の精度を向上するため
- 開発リスクを低減するため
予算を最大限に活用するため
通常、製品開発には、限られた予算が割り当てられているはずです。試作にかかるコストを削減できれば、その分をほかの開発活動に振りわけられます。
一般的に製品開発予算の30〜40%が試作関連コストであり、ここでの削減効果は大きいといえます。100万円の開発予算のうち40万円が試作費だとすると、20%の削減で8万円をほかの活動に回せる計算です。
試作コストダウンは、限られた開発予算を最大限に活用するための手段となるのです。
市場投入までの時間を短縮するため
次に、コスト効率の良い試作方法を選ぶことで、試作のサイクルも迅速に回ります。結果として、製品の市場投入までの時間を短縮できるケースも少なくありません。
市場投入の遅れは、単純に考えれば1日あたりの売上における機会損失になります。他方、競合より1か月早く市場投入できれば、その間の市場シェアを獲得できるチャンスも高まるでしょう。
試作コストダウンは開発スピードの向上にも直結し、ひいては早期の市場投入による競争優位性の確保にもつながるわけです。
競争力を強化するため
市場への投入までの時間を短縮できるだけに限らず、試作コストを削減できれば、最終製品の価格競争力を高めることもできます。開発コストが低ければ、浮いた分だけ製品価格へ反映するといった選択も可能になるからです。
競合製品が10,000円で販売している市場で、試作フェーズのコストダウンにより、同等品質で9,000円という価格設定を打ち出せるといったイメージです。実際にはこう単純ではありませんが、浮いたコストは製品で頻発する価格競争、これに対応できる余力にもなります。
量産時のコスト予測の精度を向上するため
試作段階でコストダウンを含めた管理を行えると、量産時のコスト予測もより正確になります。試作で使用する材料や工法を量産に近づけることにより、実際の製造コストをより正確に見積もれるからです。
量産コストの予測精度が上がれば、製品の収益性計算もより確実になります。ビジネス判断の精度が向上し、事業計画の信頼性は高まるはずです。
開発リスクを低減するため
最後に、低コストの試作方法を活用し、より良い設計案や材料の組み合わせを試すことでも開発リスクを分散できます。1つの方向性に全予算を投入するのではなく、複数の可能性を並行して検証できるためです。
例えば、3つの異なる設計案を低コストで試作・評価するとしましょう。「これがいいはず」という仮説で作り込み、あとから「違った」と考えた際には、修正となります(この修正が手戻り)。
一方、最初に3案くらいを小さく・安く試しておけば、良くない案を影響が小さいうちに捨て、有望なものだけにリソースを集中できます。もっとも成功確率の高い方向性を早期に見極められたとしたら、製品開発の成功確率を高める、リスクヘッジ戦略としても役割を果たすのです。
試作段階で検討できる7つのコストダウンの観点
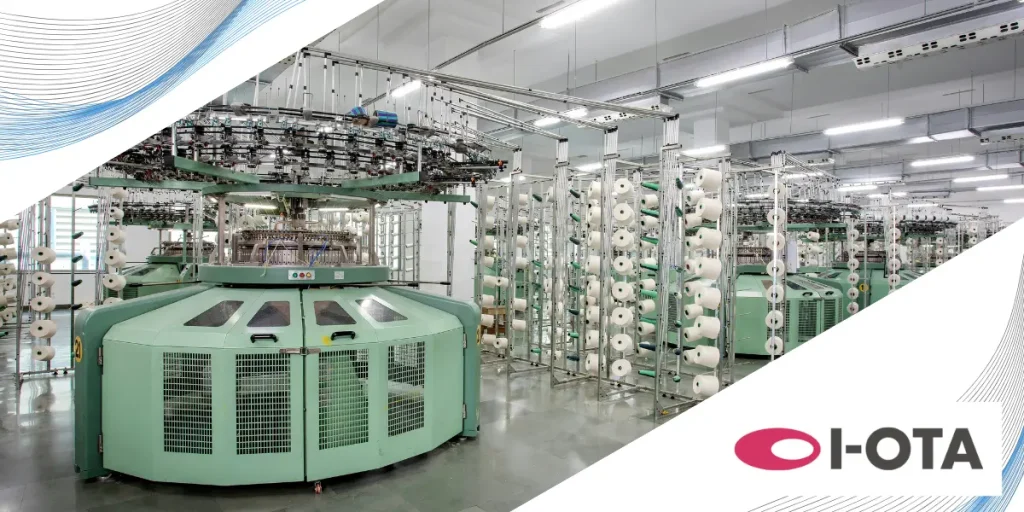
試作コストを削減するには、さまざまな観点からアプローチしなくてはなりません。以下に、試作段階で検討できる主なコストダウンの観点を紹介します。
- 金型製作費
- 材料調達コスト
- 加工工数
- 設計変更の頻度
- 試験評価費用
- 外注費
- 設備稼働コスト
金型製作費
試作段階で、コストを高める要因となるのが金型製作費です。精密な部品や複雑な形状を持つ製品では、一般的に金型費用が試作コスト全体の50%以上を占めます。
金型は一度作ると修正が難しく、設計変更のたびに新しい金型が必要になり、数十万円から数百万円と費用が増大しかねません。試作の度に新しい金型を製作していては、予算をすぐに使い果たしてしまうでしょう。
材料調達コスト
試作用の材料は少量調達となるため、量産時と比べて単価が高くなりやすいです。特殊な材料や高機能材料では、最低発注量を設定しており、必要以上の量を購入せざるを得ないケースもあります。
場合によっては、1kg当たりの単価が5〜10倍になるといったケースも想定し、試作段階でコストダウンを図るために代替材料の検討も一案です。流通性の高い材料を選択したり、複数のプロジェクトで材料を共有したりするなどの観点を持ちましょう。
加工工数
試作品の製作には、設計・プログラミング・加工・仕上げなどの工数がコストに直結します。手作業が多い試作では、技術者の人件費が割合を占めるでしょう。
- プログラミングに数時間
- 加工に数時間
- 仕上げに数時間
など、いつの間にか、1つの部品に対して合計10時間以上の工数がかかっていたとなればコストは増加します。コストダウンを目指すとはいえ、品質や実現性を加味すると、この人件費はバランス良く考えなければなりません。
設計変更の頻度
試作段階では設計変更が頻繁に発生し、その都度新たな試作を要するケースも含みます。そして、設計変更の回数が増えるほど、試作コストは比例して増加するのが一般的です。
そのため、シミュレーション技術の活用や、設計レビューの充実によって、初期設計の完成度を高める工夫も検討します。結果として、設計変更の回数が減れば、コストダウンにつながることもあります。
試験評価費用
試作品が完成したあとの性能試験や耐久試験、安全性試験などにかかる費用も無視できません。規制の厳しい業界(医療機器、自動車部品など)では、認証取得のための試験費用が高額になります。
試作の度に試験を繰り返していては、予算をすぐに使い果たしてしまうでしょう。シミュレーション技術を活用して物理試験の回数を減らしたり、試験項目を最適化したりするなど、こうした方法で費用を削減できる可能性があります。
外注費
自社に設備や技術がない場合、試作の一部または全部を外部に委託することになります。こうした外注費もコストの大部分を占め、ときには予想以上に高額になります。
なかでも、精密な金属加工や特殊な表面処理など、特定の専門業者への外注は、少量発注では割高になりやすいです。複数の外注先を比較検討したり、発注ロットをまとめたりするといったコストダウンの観点を持つ必要があります。
設備稼働コスト
試作に使用する設備の償却費や運転コスト(電力、消耗品など)も、試作コストの一部を構成します。試作のためだけに、高額な専用設備を購入した場合を考えてみましょう。
設備の稼働率が低いと、どうしても試作1個あたりのコストが高くなってしまいます。数百万円から数千万円するものであれば、年間の減価償却費だけでも相当な金額です。そのため、設備の共有化や外部サービスの活用によって、このコストを分散する考えも持ちましょう。
試作のコストダウンを実現する10のアイデア・手法
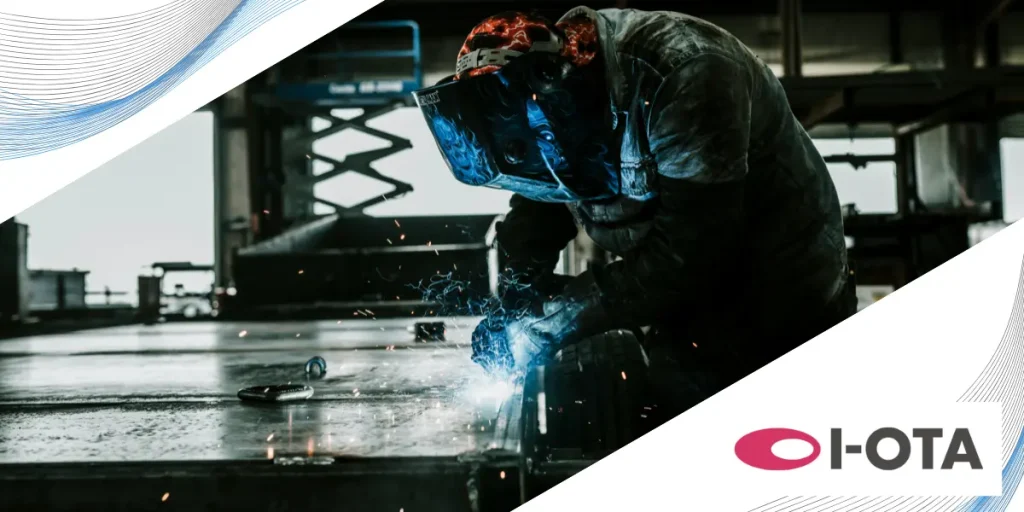
ここからは、試作コストを削減するための具体的なアイデアや手法を10個紹介します。状況に応じて組み合わせて、コストダウンを目指してください。
- 3Dプリンターを使う
- 簡易金型を採用する
- 工法転換を検討する
- 材料を最適化する
- 設計の標準化を狙う
- 試作回数を調整する
- シミュレーション技術を活用する
- 外部の設備や技術に頼る
- 試作専門業者と連携する
- 試作から量産までの一貫設計を考える
3Dプリンターを使う
3Dプリンターは、金型不要で複雑な形状も短時間で作成できる方法です。形状確認や組付け検証の段階では、材質の違いを許容できればコストダウンが可能です。
従来なら金型製作に数週間と数十万円かかっていた部品が、3Dプリンターなら数時間と数万円で試作できることも珍しくありません。複雑な内部構造を持つ部品では、その効果は顕著です。
最新の3Dプリンターでは樹脂だけでなく、金属や複合材料なども扱えるようになりました。適用範囲が広がっているのを踏まえても、試作でコストダウンを狙う切り札となる技術といえるでしょう。
簡易金型を採用する
本格的な量産金型ではなく、樹脂型やアルミ型などの簡易金型を使用できれば、金型コストも削減できます。少量の試作や形状が比較的単純な部品では、この方法が有効です。
射出成形用の量産金型が数百万円するのに対し、樹脂型なら数十万円で製作できる可能性があります。耐久性は劣りますが、数十〜数百個程度の試作であればコストダウンは十分に対応可能でしょう。
工法転換を検討する
量産時とは異なる加工方法(工法)を試作段階で採用し、初期コストを削減するアイデアもあります。具体的には、射出成形予定の部品を切削加工で試作したり、プレス加工予定の部品をレーザー加工で試作したりするなどです。
工法転換の際には、最終製品との材質や特性の違いに注意しなければなりません。射出成形品を切削加工で試作すると、内部応力や表面性状が異なるため、一部の性能評価には適さないといった具合で、専門の知識が求められます。
工法転換は試作コストダウンの有効な手段ですが、最終製品との差異を理解したうえで適用範囲を判断しましょう。
材料を最適化する
試作段階では、量産時と同じ材料にこだわらず、類似の特性を持つ代替材料を使用するのもコストダウンにつながります。特殊な高機能材料は試作段階では汎用材料に置き換え、材料コストを抑えるといった考え方です。
材料変更の際には、特性(強度、耐熱性、電気特性など)が試験目的に対して十分かを確認しましょう。すべての特性を再現する必要はなく、検証したい特性に焦点を当てた材料選択が大切です。試作のコストダウンだけを狙って、品質や性能を犠牲にしないようにしましょう。
設計の標準化を狙う
過去のプロジェクトで使用した部品や構造を再利用することで、設計工数と試作コストの削減も狙えます。特に、機構部品やコネクタなど、標準化しやすい部分に有効です。
標準部品であれば、既に検証済みのため、試作回数も減らせる利点があります。設計の標準化は、単一製品のコストダウンだけでなく、製品ファミリー全体での開発効率向上にもつながります。
加えて、異なる製品間でも共通の内部構造やインターフェースを使って、設計資産を最大限に活用できるでしょう。設計の標準化は、試作のコストダウンの基盤ともいえるアイデアです。
試作回数を調整する
試作は「必要な時に、必要な数だけ」行うという考え方が肝要です。計画的な試作スケジュールを立て、複数の検証項目をまとめて行い、試作回数を削減できます。
調整は、同じ試作品で複数の項目を検証できないだろうか、というような視点が、試作回数を減らしてコストダウンを実現するきっかけになります。試作の目的を明確にし、一度の試作で複数の課題を解決する意識を持ちましょう。
また、シミュレーションと物理試作を適切に組み合わせることも、試作回数を最適化する観点になります。
シミュレーション技術を活用する
コンピューターシミュレーションを使えば、物理的な試作の前に問題を発見し、試作回数を減らすことも可能です。構造解析、流体解析、熱解析など、さまざまなシミュレーション技術などが該当します。
シミュレーションは初期投資(ソフトウェア導入や技術者育成)が必要ですが、長期的にはコストダウン効果をもたらします。一部の製品では対応しておらず選びにくい場合もありますが、試作のコストダウンでは検討できるアイデアです。
外部の設備や技術に頼る
すべての試作工程を自社で行うのでは、膨大な時間と費用を要します。であれば、専門業者や研究機関などの外部リソースで、設備投資のコストダウンを狙いつつ、品質を保つのも一案です。
3Dプリンターサービスは、高額な設備を自社で保有せずに最新技術を活用できる好例ですし、I-OTAのようなワンストップの企業であれば各領域から技術を借りられます。
複数の外注先を比較・検討できれば、コストパフォーマンスの高い選択も可能になります。外部リソースの活用は、自社の独自の価値に注力しながら試作を実現する手段として考えましょう。
試作専門業者と連携する
試作に特化した専門業者は、試作方法や材料選定などでコストダウンを提案できるノウハウを持っています。少量多品種の試作では、専門業者の方が自社製作よりも良い場合があります。
試作に対応した専門業者は複数のクライアントの仕事を扱うため、設備の稼働率が高いです。結果として1件あたりのコストを抑えられ、依頼単価も安く済むわけです。さまざまな業界の試作経験から得た知見を活かした提案も期待できます。
試作から量産までの一貫設計を考える
試作段階から量産を見据えた設計を行い、後戻りのリスクを減らし、トータルの開発コストを削減するのもコストダウンのアイデアの1つです。平たくいえば、試作と量産で大きく設計を変更する必要がないよう、初期段階から製造性を考えるということです。
- 試作型の精度を高める
- 量産を想定した試作型で製造回数を減らす
- 試作型を流用して量産へ
上記のプロセスにより、試作から全体のコストダウンも狙います。
一貫設計のアプローチでは、試作段階で使用する材料や工法を可能な限り量産に近づけます。これにより、試作と量産の間のギャップを最小化し、移行時の予期せぬ問題発生リスクを低減できるでしょう。
試作のコストダウンで気をつけたい3つの注意点
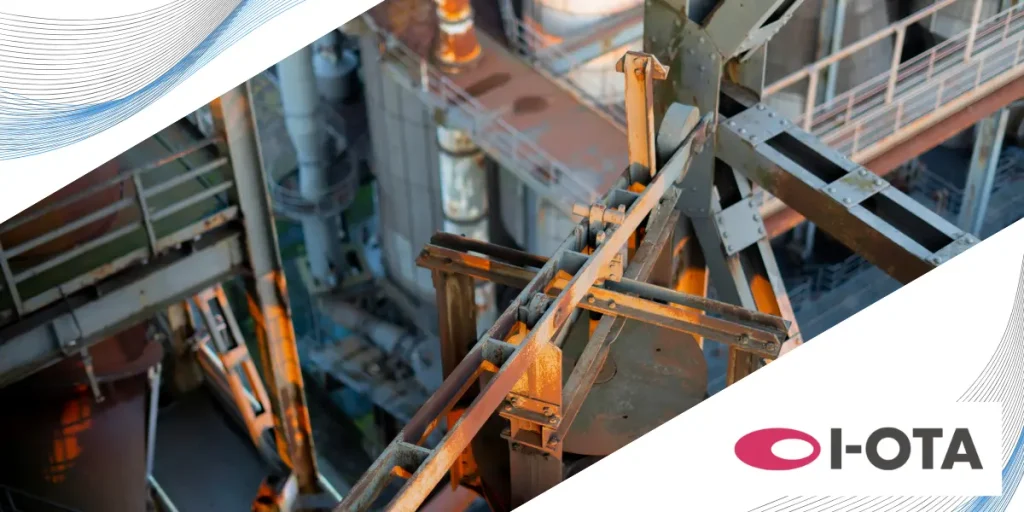
試作のコストダウンで気をつけたいのは、以下の3つです。
- 試作品の品質・精度の低下は避ける
- 量産移行時の予期せぬトラブルを想定する
- 検証範囲は制限しすぎない
試作品の品質・精度の低下は避ける
まず、コストダウンを優先するあまり、試作品の品質や精度が低下し、正確な評価ができなくなるリスクです。代替材料や、簡易的な製造方法を採用する場合に注意が必要です。
例えば、量産では金属で製造する部品を、試作段階では3Dプリンターを使って樹脂で製作したとします。これでは強度や耐熱性などの特性が異なるため、一部の性能評価には使用できません。
そのため、試作では目的を明確にし、品質要素を十分に確保したうえでコストダウンを図ることが重要です。形状確認が目的なら材質の違いは許容できますが、強度試験が目的なら材質特性の再現性は必須と考えましょう。
量産移行時の予期せぬトラブルを想定する
試作段階と量産段階で異なる材料や製造方法を採用すると、製品特性に差異が生じ、量産移行時に予期せぬ問題が発生するリスクもあります。内部応力や表面性状、寸法精度などが異なるため、組付けや機能に影響が出るといった具合です。
このことから、試作と量産の差異を事前に把握し、その影響を評価しておきましょう。材料特性の違いが製品機能にどう影響するかを理論的に検討し、必要に応じて補正係数を設定するなどの対応が有効です。
開発の後期段階では、少なくとも一部の試作品を量産と同じ材料・方法で製作し、差異の検証を行うことをおすすめします。
検証範囲は制限しすぎない
コストダウンのために試作数や試験項目を減らすと、製品の信頼性や安全性の検証が不十分になりやすいです。安全性や耐久性に関わる検証であれば、省略すべきではありません。
耐久試験の回数を減らしたり、極端な環境条件での試験を省略したりすると、結果として市場投入後に予期せぬ不具合を引き起こすリスクが高まります。重要度に応じた試験項目の優先順位付けを行い、検証は確実に実施しましょう。
安全性や基本機能に関わる試験は必ず実施し、そのうえで、オプション機能や極端な使用条件に関する試験は状況に応じて判断するといった優先順位付けが有効です。シミュレーション技術を活用した物理試験の補完も検討可能です。
試作のコストダウンに悩んだら外部パートナーとの連携が重要
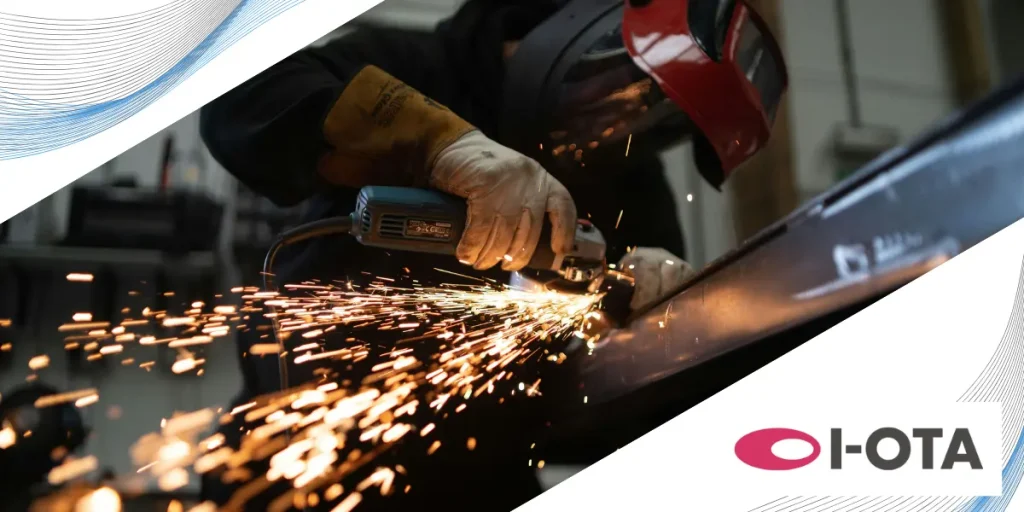
試作コストダウンを自社だけで進めるのではなく、専門の外部パートナーと連携することで、より効果を得られます。
- 不足している知識を補える
- 設備投資を抑制できる
- 組織全体を効率化できる
- 多様な工法の選択肢を得られる
など、さまざまなメリットがあります。特に、試作の頻度が少ない企業や、専門的な製造技術を持たない企業にとって価値があります。
自社のコアコンピタンスに集中しながら、試作の効率と品質を高めるためには、適切な外部パートナーとの連携が重要です。自社リソースの最適化と、試作品質の向上を同時に実現する方法としてぜひ検討してください。
関連記事:製造アウトソーシングとは?委託可能な業務や利用のメリット・デメリットを解説
まとめ:試作のコストダウンならI-OTAへ
試作段階では3Dプリンター活用、樹脂型採用、工法転換、材料最適化などの手法を組み合わせれば、品質を維持しながらコストダウンが可能です。
ただし、品質低下や量産移行時のトラブル、検証不足といったリスクにも注意が必要です。試作のコストダウンを実現するには、目的を明確にし、適切な手法を選びましょう。
I-OTAでは、製造業に精通した専門家が、お客様の試作ニーズに合わせた最適なコストダウン提案を行っています。大田区の製造ネットワークを活かした一貫生産体制で、高品質かつコスト効率の良い試作をサポートしますので、試作コストでお悩みの方は、ぜひI-OTAにご相談ください。
>>モノづくりの経験が豊富なI-OTAワンストップ解決を依頼する
よくある質問(FAQ)
コストダウンとは何ですか?
コストダウンとは、製品やサービスの品質や機能を維持・向上しながら、製造・提供にかかる費用を削減することを指します。経費削減ではなく、効率化や最適化によって無駄を省き、本質的な価値を損なわずにコストを下げる取り組みです。
金型費用の削減、材料の最適化、工法転換、工程集約などの手法を通じて、品質を確保しながら試作にかかる費用の削減を目指します。「安かろう悪かろう」ではなく、必要な品質と機能を維持したうえで、不要なコストを削減するという考え方です。
コストリダクションとコストダウンの違いは何ですか?
コストダウンとコストリダクションは、日常的には同じ意味で使うことが多いですが、厳密には若干のニュアンスの違いがあります。
コストダウンとは、主に既存の製品や工程の効率化や最適化によってコストを下げることです。材料の変更、工程の集約、外注先の見直しなどが該当します。
一方、コストリダクションは、より計画的・体系的なコストダウンを狙う活動を指します。設計段階からのコストダウン(デザイン・フォー・コスト)、サプライチェーン全体の最適化、長期的な投資によるコスト構造の改革などが該当するでしょう。
コストダウンとVEの違いは何ですか?
コストダウンとVE(Value Engineering:価値工学)は関連する概念ですが、アプローチと目的に違いがあります。
コストダウンは、主にコストの削減に焦点を当てた活動であり、現状の品質や機能を維持しながらコストを下げることを目指します。具体的には、同じ機能を持つより安価な材料への変更や、製造工程の効率化などです。
一方、VEは「価値」の向上に焦点を当てた活動であり、価値を「機能÷コスト」と定義します。コストを下げるだけでなく、機能を向上することでも価値を高められます。
試作の目的は何ですか?
試作の目的は多岐にわたりますが、主に以下のような目的があります。
- 形状や外観の確認
- 機能や性能の検証
- 製造性の検証
- 市場調査や顧客フィードバック
- 認証や規格適合性の確認
試作コストダウンを考える際には、この目的を明確にし、その目的に必要十分な品質レベルの試作方法を選ぶことが重要です。試作の目的を明確にすることが、試作コストダウンの第一歩となるでしょう。