製造アウトソーシングとは、自社の製造工程の一部または全部を外部企業へ委託する方法を指します。
うまく活用できれば、自社のコア業務に経営資源を集中させながら、製造工程の効率化とコスト削減を同時に実現できます。しかし、闇雲にアウトソーシングを導入しても、期待した効果が得られないばかりか、かえってコストが増加してしまうケースもあります。
そこで本記事では、製造アウトソーシングの基礎知識から、メリット・デメリット、成功のポイントまで詳しく解説します。「どの業務を委託すべきか」「どのように業者を選定すべきか」などにも触れるため、ぜひ最後までご一読ください。
製造アウトソーシングとは
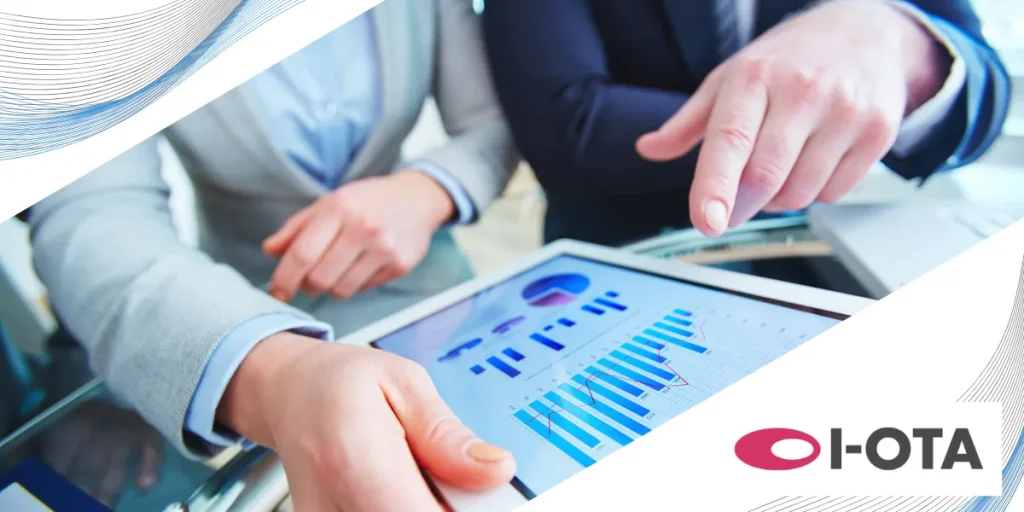
製造アウトソーシングとは、自社における製造工程の一部、または全部を外部の企業に委託する方法のことです。自社の強みを活かせる工程は内製化し、それ以外の工程を外部委託と区切ることで経営の効率化を図れます。
対象は、部品の組み立てから原材料の加工、検品作業まで多岐にわたり、主に限られた経営資源をコア事業に集中させるために活用します。グローバル競争の激化や人材不足、技術の高度化といった課題を解決するためにも、製造アウトソーシングは役立ちます。
アウトソーシングと人材派遣との違い
製造アウトソーシングと人材派遣の違いは「指揮命令権」にあります。
アウトソーシングでは、委託先企業が独自の判断で業務を遂行し、成果物を納品します。
製品の検査工程をアウトソーシングする場合、委託先企業は独自の検査基準や手順で業務を行い、合格品のみを納品するのです。結果、業務委託契約に基づき、完成した仕事に対して報酬が支払われます。
一方で、人材派遣では派遣された人材は依頼企業の指示のもとで働きます。
派遣された検査員は、依頼企業の基準や指示にしたがって検査を行います。そのため、労働者派遣契約に基づき、派遣社員の労働時間に応じて料金が発生します。
アウトソーシングとOEMとの違い
アウトソーシングとOEMの主な違いは、「形態」にあります。
アウトソーシングは特定の製造工程のみを外部委託する形態です。
アパレルメーカーがOEMを活用する場合、縫製や裁断といった特定工程のみを外部に委託し、製品全体の企画や品質管理は自社で行います。つまり、部分的な工程委託が中心です。
一方、OEMは発注元企業のブランドで製品を製造する委託形態であり、製品の企画や仕様は発注元が決定します。委託先工場は発注元ブランドの衣服を製造するため、成品の製造委託となります。
製造アウトソーシングに依頼できることの例
製造アウトソーシングに依頼できることの例には、以下が挙げられます。
- 部品の組み立て
- 原材料・半製品の加工
- 検査・検品
- プレス加工
部品の組み立て
製造アウトソーシングの代表的な委託内容が、部品の組み立てです。専門業者は豊富な経験と専用設備を持っているため、高品質な組立作業を実現できます。
主に、電子機器や自動車部品など、複雑な組立工程が必要な製品において効果を発揮します。組立工程をアウトソーシングできれば、製品の品質向上だけでなく、生産ラインの効率化も実現しやすいです。
また、部品の調達から最終組立までを一括で委託した場合は、サプライチェーン全体の最適化も可能になります。
原材料・半製品の加工
原材料や半製品の加工工程も、高度な技術と専用の設備が必要となるため、アウトソーシングに適しています。以下の例のように素材に応じた専門的な加工技術を持つ業者に委託し、高品質な製品を生産できるためです。
- 金属の切削加工
- プラスチック成形
- 木材加工
結果として自社で高額な加工設備を導入する必要もなく、設備投資や保守管理のコストまで抑えられる点もメリットです。
検査・検品
製品の品質を保証する検査・検品工程も、アウトソーシングの対象として挙げられます。専門業者は、検査機器と熟練した検査員を業界に応じた体制で有しています。
外観検査、寸法測定、機能テストなど、製品特性に応じた適切な検査方法を提案しつつ、高精度な品質管理を実現できます。また、不良品の発見だけでなく、品質データの収集・分析まで一括して依頼できるため、継続的な品質改善にも役立ちます。
プレス加工
プレス加工とは、金属材料を型で打ち抜いたり成形したりする加工方法のことで、自動車部品や電機部品の製造に欠かせない工程です。自社でプレス設備を導入するよりも、専門業者へのアウトソーシングに切り替えれば、設備投資を抑えながら高品質な加工を実現できます。
専門のプレス加工業者は、大型プレス機械や精密な金型を保有しており、高精度な加工を実現できます。また、材料の選定から金型設計、後処理まで一貫した対応が可能です。
製造アウトソーシングを依頼する5つのメリット
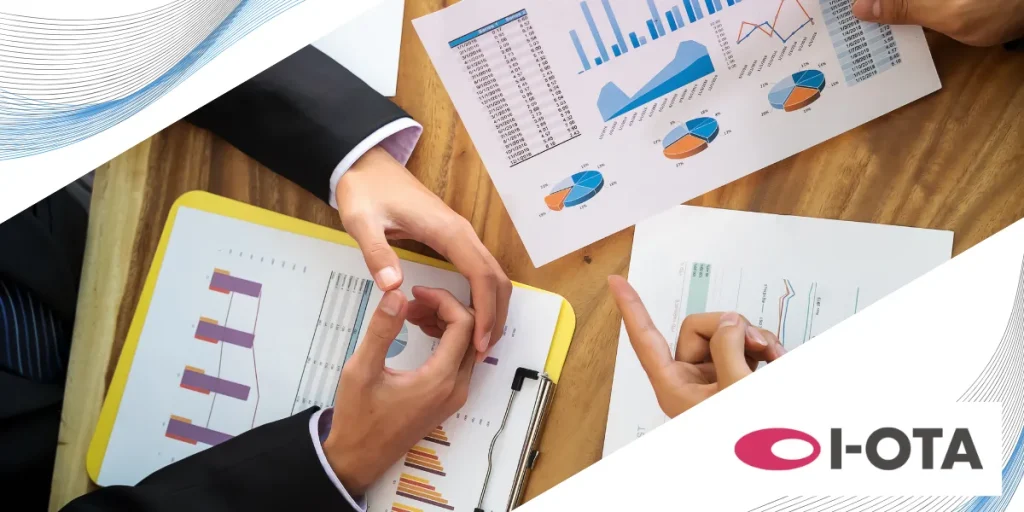
製造アウトソーシングを依頼するメリットは、以下の5つです。
- コア業務へリソースを割ける
- コストを削減できる
- 人手不足が改善する
- 生産性が向上する
- 品質が高まる
コア業務へリソースを割ける
製造アウトソーシングのメリットは、自社の経営資源をコア業務に集中できることです。製造工程の一部を外部委託できれば、これまで製造に割いていた人材・設備・資金などを、商品開発や営業活動といった収益性の高い業務に振り向けられます。
特に中小企業では、限られた経営資源をどのように活用し、どう活かすかに注力しなければなりません。その際、製造アウトソーシングによって、自社の強みを活かせる分野により多くのリソースを投入できます。
コストを削減できる
製造アウトソーシングでは、固定費を変動費化できることでコスト削減も可能です。製造設備の購入・メンテナンス費用、作業員の人件費、工場の賃借料など、これまで固定的にかかっていたコストを、必要な分だけ外部に支払う形に変更できます。
また、製造量に応じて委託量を調整できるため、需要の変動にも柔軟に対応が可能です。場合によっては、専門業者の持つスケールメリットを活用によって、材料調達コストからの削減も期待できます。
人手不足が改善する
製造業における慢性的な人手不足の解消においても、製造アウトソーシングは解決策となります。
通常、暗黙知から形式知への落とし込み、新たな人材を育成するまでには相当な時間を要します。場合によっては、何度も繰り返して感覚を体で覚えてもらうといった慣習もあり、難航しやすいです。
こうした熟練工の確保や技能継承に課題を抱える企業にとって、アウトソーシング業者の持つ人材プールは魅力です。また、繁忙期と閑散期の人員調整も、委託で柔軟に対応できます。
将来的に見れば、採用・教育にかかるコストや時間も削減でき、人材確保の負担の軽減も期待できます。
生産性が向上する
製造アウトソーシング業者は、すでに依頼を受けられる準備を済ませており、製造設備や生産システムなどのインフラを保有しています。委託が保有するインフラを委託によって活用できれば、自社で製造するよりも高い生産性を実現しやすいです。
業者の持つ製造ノウハウや改善提案により、依頼前に整理した製造プロセス全体の最適化も期待できます。複数の工程を一括して委託できる業者であれば、製造リードタイムそのものの短縮も可能になります。
品質が高まる
製造アウトソーシング業者の持つ専門的な品質管理システムや検査体制を活用し、製品品質の向上と安定化も図れます。一定の成果を上げているものの、さらにブラッシュアップしたいと考えた際に有効です。
業者は複数の取引先の製造を手がけており、その経験から得られた品質改善のノウハウを活用できます。品質トラブルが発生した際も、専門家による迅速な対応が期待でき、品質のボトムアップを目指せます。
製造アウトソーシングを依頼する3つのデメリット
製造アウトソーシングにはメリットが多いものの、以下に挙げた3つのデメリットも存在します。
- コスト削減を確約できない
- ノウハウが自社に蓄積されない
- 組織体制を頻繁に変更しにくい
コスト削減を確約できない
製造アウトソーシングは、人件費や設備投資の削減が期待できる一方で、必ずしもコスト削減を保証するものではありません。なぜなら、アウトソーシング自体の目的が単なるコスト削減だけではなく、短期的にはコストが増加する可能性もあるためです。
むしろ、効率化を通じた自社のコア事業への経営資源の再配分こそが、製造アウトソーシングの本質的な役割です。過程では、委託先との連携や品質管理のために新たな人員配置が必要になったり、アウトソーシング会社への業務移管時に想定以上の工数がかかったりするケースも少なくありません。
依頼する際には長期的な視点で、コア事業への集中による競争力強化というメリットと、総合的なコストのバランスを見極めることが重要です。
ノウハウが自社に蓄積されない
製造工程を外部委託する際には、その工程に関する技術やノウハウが自社内に蓄積されにくくなります。生産技術や品質管理のノウハウは競争力の源泉となるため、一時的にアウトソーシングを利用し、最終的に内製化するといったケースでは課題となります。
また、委託先との業務上のやり取りにおいて、製造に関する機密情報や技術情報を共有する際の情報漏えいのリスクも考慮しなければなりません。リスクを最小限に抑えるためには、アウトソーシングする工程の選定を慎重に行い、将来的に自社の競争力となり得る工程については内製化を維持するという判断も必要です。
組織体制を頻繁に変更しにくい
製造アウトソーシングを導入すると、組織体制の変更に際して従来以上の調整が必要になる可能性もあります。自社内での変更と比べて、委託先への説明や対応可否の確認など、1社分の工数が追加で発生するためです。
生産量の急な変更や製造工程の見直しが必要になった場合、委託先との契約内容の変更や新たな体制の構築に時間がかかります。委託先との密なコミュニケーション体制を構築し、変更の可能性がある場合は早めに相談するなど、柔軟な対応が可能な関係性を築いておきましょう。
製造アウトソーシングを成功させるための3つのポイント
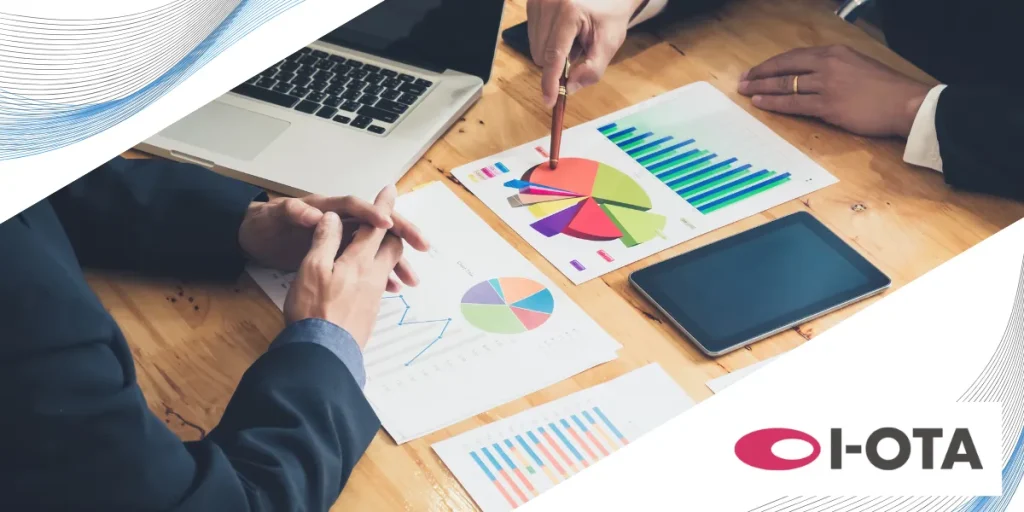
製造アウトソーシングを成功させるために押さえたいポイントは、以下の3つです。
- 業務内容は最初から丁寧に洗い出す
- 品質管理の基準等を明確にしておく
- コミュニケーションを定期的に取る
業務内容は最初から丁寧に洗い出す
製造アウトソーシングを成功させるためには、委託する業務内容を事前に明確化してください。業務の切り分けが不明確だと、かえって工程が煩雑化してしまう可能性があるからです。
まず、自社の製造工程を「コア業務」と「非コア業務」に分類します。その上で、非コア業務の中から、アウトソーシングに適した工程を選定しましょう。
実績のある委託先であれば、業務の洗い出しを一緒に進めることも可能です。協議しながら、業務の範囲や責任の所在、予期せぬトラブルの対応についても、事前に取り決めておくことで、スムーズに業務移管できます。
品質管理の基準等を明確にしておく
製造アウトソーシングでは、品質管理の基準を明確に定めることも、「コスト削減を確約できない」「ノウハウが蓄積されない」といったデメリットを最小限に抑えるポイントです。自社で行っていた品質管理が委託先に移るため、品質基準や管理方法に具体的な数値目標を含めて合意しましょう。
特に重要なのが、SLA(サービスレベルアグリーメント)の締結です。
SLAでは、製品の品質基準や納期、不良品が発生した際の対応など、具体的なサービス内容を明文化します。また、機密情報の取り扱いについても、明確なルールを設定しておきましょう。
コミュニケーションを定期的に取る
製造アウトソーシングを適切に機能させるには、委託先との定期的なコミュニケーションが欠かせません。月次や週次での進捗会議を設定し、課題や改善点を共有できれば「ノウハウが自社に蓄積されない」というデメリットも解消できます。
議題においては、以下の3点について定期的な確認を行うことを基本としてみましょう。
- 品質状況の確認
- コスト管理の状況
- 工程改善の提案
また、委託先からの改善提案を積極的に取り入れることで、製造プロセスの最適化も図れます。「組織体制を頻繁に変更しにくい」というデメリットも、委託先との密なコミュニケーションを通じて、柔軟な対応が可能となります。
製造アウトソーシング企業を選ぶ基準
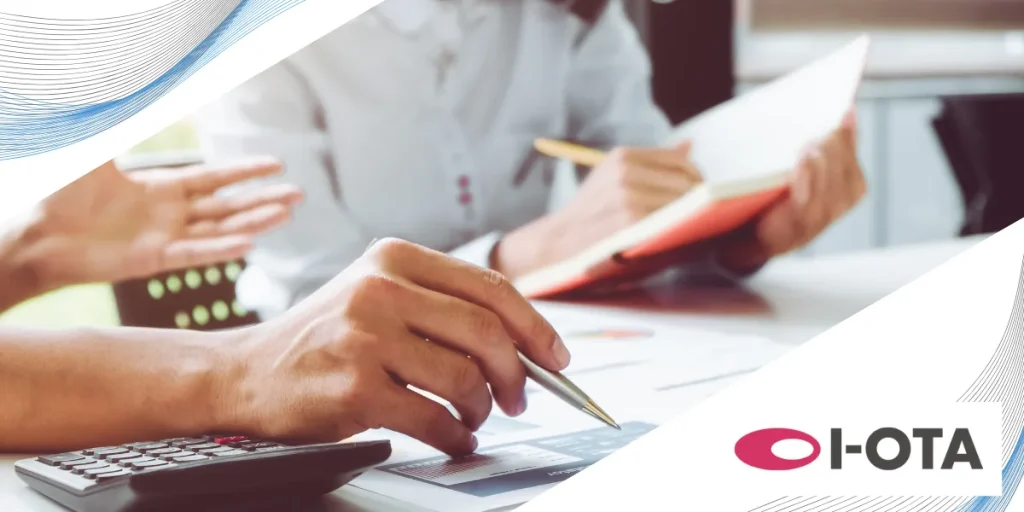
製造アウトソーシング企業を選ぶ際、多くの方は技術力や価格、納期といった複数の基準で比較検討します。しかし、実際に選ぼうと思うと具体的な数値がなかったり、情報を得られなかったりするケースがほとんどです。
そこで重要視してほしいのが、「現在の状態からでも細かく相談できること」です。なぜなら、製造プロセスは製品によって変化するものであり、対話のなかで気づく課題も多くあるからです。
図面の段階から量産化まで、トータルしてきめ細かなコミュニケーションを通じて最適な解決策を見出せる企業こそが、思い描くアウトソーシングを実現しやすい企業の形です。
まずは、一緒にいま目の前にある課題から考えてみませんか?
I-OTAでは、図面からアイデアまで、すべての製造相談に対応できる体制を整えています。それは、私たちが常にお客様と同じ目線に立ち、課題を共に考え抜く姿勢を持っているからです。
まずは気軽にご相談ください。製造の専門家が、お客様の事業フェーズや現状に合わせてご提案します。
製造業アウトソーシングの導入シーンの例
製造業アウトソーシングにおける主な導入シーンは、以下の3つです。
- 製造過程を部分的に委託したい
- 製造ライン別に委託したい
- すべての製造業務を委託したい
製造過程を部分的に委託したい
製造工程の一部をアウトソーシングすると、自社のコア業務に集中できます。
例えば、検品・検査工程のみを委託する場合、専門性の高い外部の目による品質管理が実現できます。また、設備投資や人材育成のコストを抑えながら、高い品質基準を維持できるでしょう。
部分委託は、自社の強みをいかしながら弱みを補完する戦略的な選択肢です。特に中小企業では、専門性の高い工程や季節変動の大きい工程を部分的に委託し、経営の安定化を図れます。
製造ライン別に委託したい
製造ラインごとの委託は、生産体制の最適化を目指す企業に適しています。主力製品のラインは自社で運営しながら、新製品や特殊製品のラインを委託するといった使い分けが可能です。
同ケースでは、設備投資リスクを抑えつつ、市場ニーズに柔軟に対応できる生産体制も構築できます。また、ライン別委託では、製造工程全体の管理から人材育成まで一括して外部に任せられ、自社の管理負担まで軽減できます。
すべての製造業務を委託したい
製造業務の全面委託は、自社をファブレス企業として再定義する選択肢です。製品の企画・開発に経営資源を集中させ、製造はすべて外部パートナーに任せることで、市場の変化への対応力を高められます。
全面委託のメリットは、固定費の変動費化による経営における柔軟性の向上です。ただし、品質管理体制の構築や知的財産の保護など、委託先との綿密な連携は不可欠です。製造ノウハウの蓄積方法についても、長期的な視点で検討しましょう。
製造アウトソーシングの相談はI-OTAへ
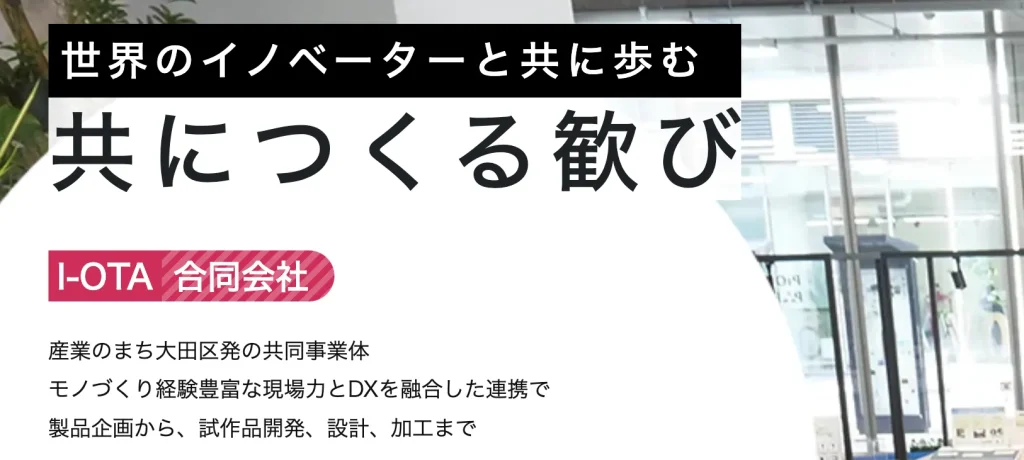
I-OTAでは、製品企画から試作品開発、設計、加工までをワンストップで提供できる体制と、お客様との対話を重視した製品開発アプローチにより、ご要望に最適な製造アウトソーシングのプランを提案いたします。
これまで、自宅用サウナストーブの開発や次世代型農耕機の試作など、多岐にわたるプロジェクトを手がけてきました。こうした経験を踏まえ、日本有数のモノづくり集積地である大田区を拠点に、豊富な製造実績を持つ技術者集団がお客様の課題に向き合います。
目の前にある課題へ悩む前に、専門家に相談しながら一緒に解決を目指しませんか?
製造アウトソーシングの課題解決へ向けた第一歩を、I-OTAと共に踏み出しましょう。まずはお気軽にご相談ください。
【今すぐ無料相談】
まとめ
製造アウトソーシングとは、自社における製造工程の一部、または全部を外部の企業に委託する方法を指します。成功のカギは、自社のコア業務を見極め、それ以外の工程を適切に外部委託できるかどうかです。
まず自社の製造工程において、「コア業務」と「非コア業務」への分類からはじめましょう。その上で、以下の3ステップで導入を検討します。
- 委託する業務範囲の明確化
- 最適な委託先の選定
- 運用体制の構築
製造アウトソーシングの成否は、導入前の綿密な計画と、導入後の適切な管理にかかっています。自社の状況を客観的に分析し、長期的な視点で製造戦略を構築して競争力の向上と持続的な成長を実現しましょう。