装置の設計は、製品の品質や生産効率に直結する工程です。設計段階で適切な検討を行わないと、後工程での問題発生や予算超過、納期遅延などのリスクが高まります。
そこで本記事では、装置設計の手順から重要なポイント、制約条件、よくある失敗事例まで、設計担当者が知っておくべき情報を体系的に解説します。これから装置設計に取り組む方や、設計プロセスの改善を検討している方は、ぜひ参考にしてください。
装置設計とは
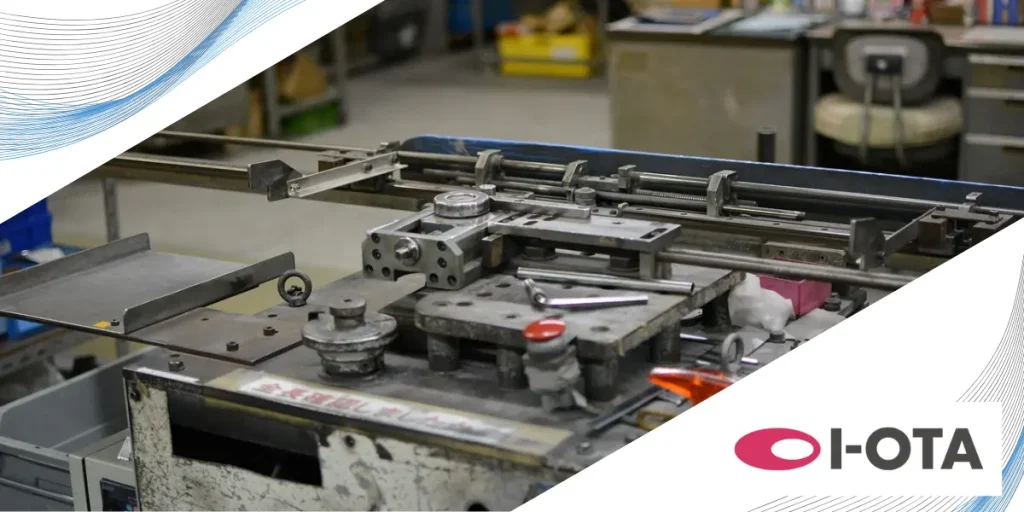
装置設計とは、特定の目的や機能を実現するための機械システムを構築するプロセスのことです。個々の機能にあった役割を持ったユニットの集合体が装置であり、それぞれが連携して全体として目的の機能を果たします。
装置の設計手順における重要ポイント
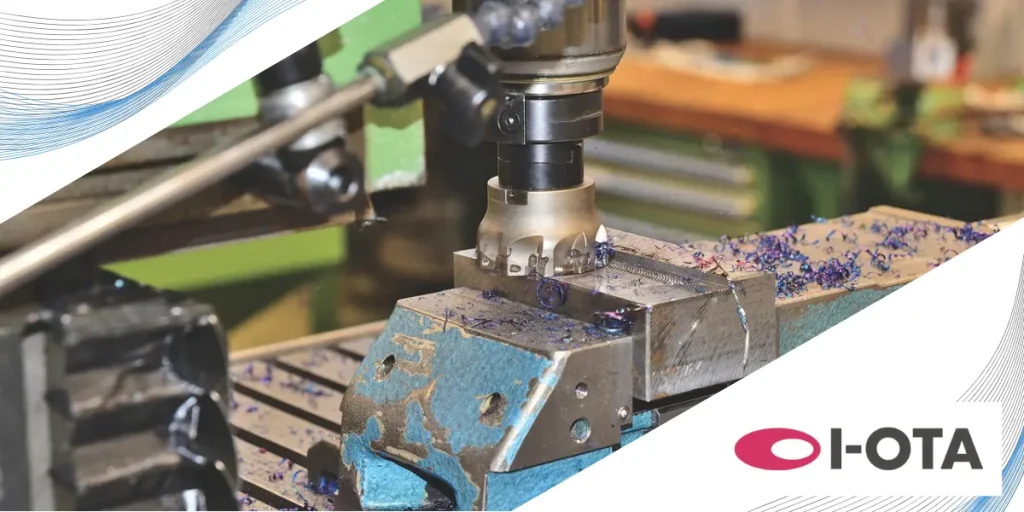
装置設計は、以下の4つのフェーズにわけられ、各段階で押さえるべきポイントが異なります。
- 要件定義
- 構想設計
- 基本設計
- 詳細設計
要件定義
要件定義は装置設計の出発点であり、装置に求める以下の要件を明確にする段階です。
- 機能
- 性能
- サイズ
- コスト
- 安全性
例えば「1時間あたり100個の生産能力」「不良率1%以下」「設置スペース2m×3m以内」といった明確で具体的な目標を定めます。
要件定義では、お客様や関係部署からの要望を漏れなく収集し、優先順位をつけることがポイントです。「何を実現したいのか」を具体的かつ、測定可能な形で明確にできれば、後の設計プロセスもスムーズに進みます。
構想設計
構想設計では、装置のコンセプトや基本的な構造、動作原理、つまり「どのような方法で要件を満たすか」というアプローチを決定します。「ロボットを使うか専用機を開発するか」「回転式にするか直線式にするか」といった方向性の大枠を決める段階です。
この段階では、複数の選択肢を比較検討し、もっとも適した方法を選ぶことがポイントです。判断次第では後工程に影響するため、過去の知見や関係者との十分な協議にもとづくことが大切です。構想設計は装置の「骨格」を決めるプロセスであり、ここでの選択は装置の性能や製造コストをも左右する点に留意してください。
基本設計
基本設計では、構想をCADなどを使って具体的な形にし、実現性を検証します。いわば装置の「骨組み」で、以下の要素を具体化して全体の構造を決める段階です。
- 主要部品の配置や寸法
- 動作シーケンス
- 制御方法
- 部品同士の干渉チェック
- 強度計算など
この基本設計のポイントは、各部品の関係性や動作の流れを明確にし、設計の妥当性を確認する点です。問題点を発見し修正できれば、後工程での変更を防げます。「構想を具体的な形にする」ことに集中し、細部よりも全体のバランスと機能性を重視しましょう。
詳細設計
詳細設計では、製品を構成する個々の部品の材料、寸法、公差、加工方法などを具体的に決定します。「この穴の公差は±0.01mm」「表面処理はアルマイト処理」といった細部の仕様を決める段階です。
この段階では、以下の点に注意が必要です。
- 組み立て順序の考慮
- メンテナンス性
- コスト削減の工夫
詳細設計は装置の「肉付け」を行うプロセスで、ポイントは製造性やメンテナンス性を考慮した実用的な設計を行うことです。この段階での少しの違いが、最終的な品質や製造コストに影響を与えるためです。「実際に製造できる形に仕上げる」ことが重要であり、製造現場の意見を取り入れながら現実的な設計を行いましょう。
装置の設計前に把握すべきユニットにおける5つの制約条件
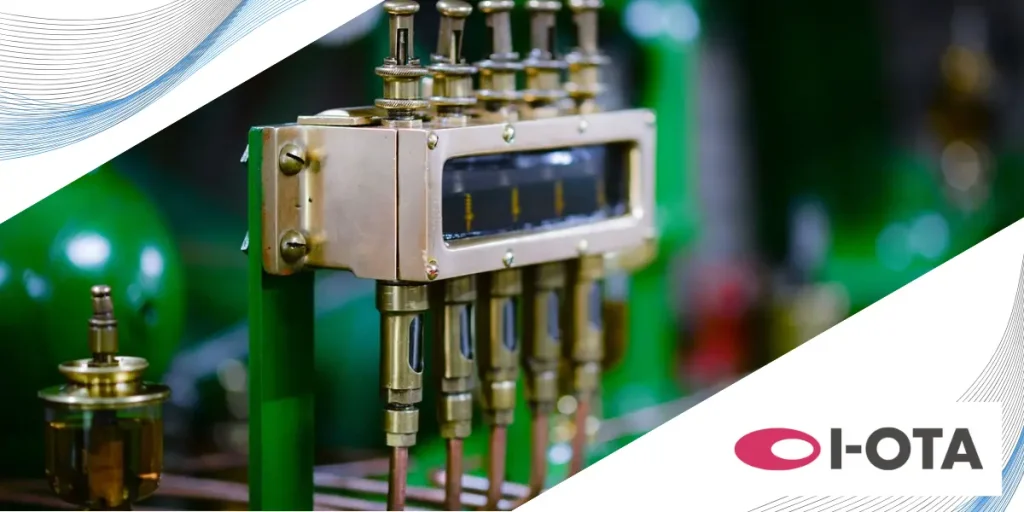
装置の設計前に把握すべきユニットにおける制約条件は、以下のとおりです。
- 予算
- スケジュール
- ユーティリティ
- 互換性
- 法規制・安全基準
制約を無視した設計は、実現不可能な「絵に描いた餅」になってしまいます。設計の「ガードレール」だと考えて、そのなかで最大限の性能を発揮する装置を設計しましょう。
予算
1つ目の制約が、予算です。
装置開発には、以下のようなさまざまな費用が発生します。
- 設計費用
- 導入費用
- 工場改修費
予算という制約は、設計の自由度を制限する一方で、創意工夫を促す要因にもなります。とはいえ、あまりに予算が限られている場合は、段階的な導入や必要最小限の機能に絞った設計も検討すべきです。
予算の制約は「限られた資源で効果を得る」という設計の本質的な課題に直結します。コストと機能のバランスを取りながら、効果を生む投資計画を立てることを意識しましょう。単なる制限ではなく、高効率な設計を促す要因として捉え、創意工夫の機会と考えることが大切です。
スケジュール
2つ目の制約が、スケジュールです。
装置開発は市場ニーズや生産計画に合わせた納期設定が求められるため、一定の期間を要します。納期を守るためには、早期に設計目標や制約条件を明確にし、無駄な修正や再設計を最小限に抑えなければなりません。
この点において、スケジュール管理は「時間」という限られたリソースを最大限に役立てる戦略です。だからこそ、プロジェクト全体のスケジュールを見据え、各工程に適切な時間を配分してください。試作や評価に十分な時間を確保できれば、量産段階での問題を未然に防げます。
ユーティリティ
3つ目の制約が、ユーティリティ(設備や資源)です。
- 新しい装置を設置するスペース
- 利用可能な電力
- 圧縮空気
- 水
など、装置の物理的な制限だけでなく、運用コストにも影響します。
例えば、天井高が3mしかない工場に4mの装置は設置できませんし、100Vの電源しかない場所で200Vの装置は使えません。環境や状況に適合しない設計は、いくら性能が良くても実用化できないのは明白です。
ユーティリティの制限においては、既存の工場レイアウトや設備容量を確認し、それに合わせた装置設計を行うことがポイントです。「現実の環境に適合した設計」を行うための条件だと考えて、実用性の高い装置設計に仕上げましょう。
互換性
4つ目の制約が、互換性です。
新しい装置は既存の生産ラインや設備と連携して動作することが多いため、互換性の確保は必須要件です。
- 前後の工程との接続方法
- 制御システムの通信規格
- 操作インターフェースの統一
などの互換性はよくある例です。この互換性の制約は「システム全体のなかでの調和」を考える機会です。孤立した装置ではなく、生産システム全体の一部として機能する装置を設計する視点を持ちましょう。
既存設備のデータフォーマットや通信プロトコルを調査し、それに合わせて設計できれば、新しい装置が既存システムと協調して動作できます。互換性を考慮した設計は、導入時のトラブルを減らし、運用の効率化にもつながります。
法規制・安全基準
最後の制約が、法規制・安全基準です。
業界によって異なる規制があり、以下のように適用となる基準が変わってきます。食品機械であればFDA基準がありますし、医療機器ならISO 13485、一般機械だとCEマーキングといった具合です。
設計の初期段階から適用となる法規制を調査し、材料選定や安全機構の組み込みを行うことがポイントです。法規制や安全基準を無視した設計は、市場に出すことができないだけでなく、事故や法的問題を引き起こす可能性もあります。
また、安全基準は「最低限クリアすべき条件」ではなく、「ユーザーの安全を守るための指針」として捉え、積極的に取り入れることが大切です。「社会的責任を果たす設計」を行うためと位置付け、持続可能な製品開発につなげましょう。
装置の設計で全体構成を決定する4つのポイント
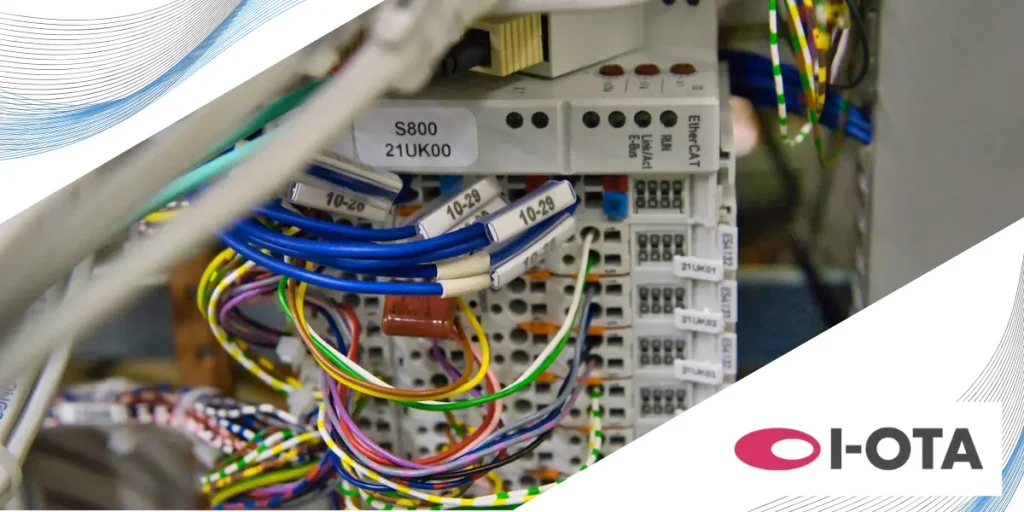
装置構成の決定は「設計の骨格づくり」であり、この段階での判断が後工程に影響する点はすでにお伝えしたとおりです。そのうえで全体構成を決める際には、以下の4つのポイントを考えます。
- 全体をどう分割するか
- 部品をどう送るか
- 部品をどう供給するか
- 部品をどう加工するか
全体をどう分割するか
装置の全体構成を決める際は、「必要な機能を最小限の構成で実現する」という考え方が基本です。複雑な工程を分解する際は、まず「入力→処理→出力」という基本構造で考えるとわかりやすくなります。
例えば、組み立て工程なら「部品供給→位置合わせ→結合→検査→排出」といった具合に分割できます。各動作の開始条件と終了条件を明確にし、前後の動作との関連性を整理しておくことがポイントです。
各動作の所要時間やタイミングを考慮し、全体のサイクルタイムが最短になるように調整するのも有効です。動作の分割が適切であれば、後の設計変更にも柔軟に対応できます。全体の分割は「複雑な問題を単純化する」プロセスですので、適切な分割によって設計の見通しが良くなれば、開発の効率も高められます。
部品をどう送るか
送り方式を選ぶとき、あなたは「どの方式がもっとも効率的か」と考えたことはありませんか?送り方式には主に「間欠送り」と「連続送り」の2つがあります。
間欠送り(インターミッテント方式)は、部品を一時停止させながら送る方式で、精密な位置決めを要する作業に適しています。一方、連続送り(コンティニュアス方式)は、部品を停止させずに連続的に送る方式で、高速処理を求める場合に適合します。
- 製品の大きさ
- 製品の重量
- 製品の形状
- 求めるレベルの精度
- 目標サイクルタイム
などを総合的に考慮して送り方式を選してください。小さな電子部品の実装だから間欠送り、ボトルの充填ラインであれば連続送り、というように装置ではどちらの方式が適しているか考えてください。製品特性と処理内容を考慮して、最適な送り方式を選ぶことで、装置の性能も変わってくるでしょう。
部品をどう供給するか
部材供給方式は「装置の入口」にあたり、装置の稼働効率に影響する要因です。適切な供給方式を選ぶことで、安定した装置運用が可能になります。
主な供給方式には、以下のような選択肢があります。
供給方式 | 特徴 | 適している部材 |
---|---|---|
パーツフィーダー | 振動で部品を整列させる | 小型の均一部品(ネジ、ナットなど) |
マガジン方式 | 積み重ねた部品を順に供給 | 平板状の部品、積み重ね可能な部品 |
パレット方式 | 専用トレイに配置した部品を供給 | 形状が複雑な部品、向きが重要な部品 |
ロボットピッキング | ロボットが視覚で認識して取りだす | 不規則に配置された部品、多品種の部品 |
例えば、小さなネジなら振動式パーツフィーダーの効率が良いですが、形状が複雑で向きも重要な部品ならパレット方式やロボットピッキングが適しています。
この場合、部材の形状、サイズ、供給速度、コストなどを考慮して最適な供給方式を決定するのがポイントです。供給がスムーズでなければ、装置全体の効率が低下してしまいますので、マッチする供給方法を何度か試すと良いでしょう。
部品をどう加工するか
加工方式の選定は、「目的に合った手段を選ぶ」プロセスです。切削、プレス、溶接、組み立て、検査などから最適な加工方式を選ぶことで、効率を高めつつ高品質な生産が可能になります。
加工方式を選定する際は、求めるレベルの精度、生産量、材料特性、コストなどを総合的に考えることがポイントです。例えば、高精度を求める場合はCNC加工が適していますが、大量生産ならプレス加工を選ぶといった具合です。
加工方式によって要する設備や専門知識も異なり、溶接プロセスでは温度管理や材料の熱変形を考えなければなりません。組み立てプロセスでは、部材のハンドリングと位置決めも考慮できると良いでしょう。
装置の設計で機構を選定する6つの検討ポイント
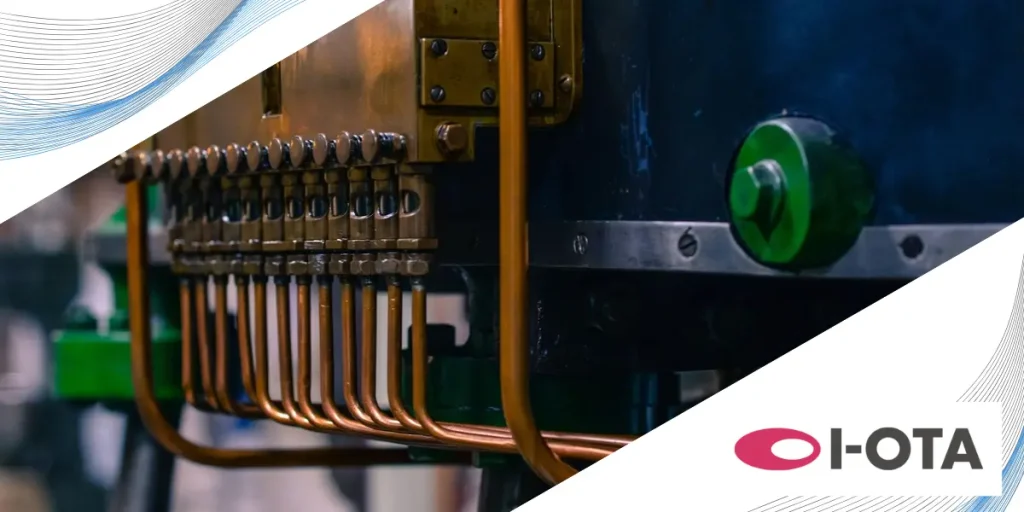
機構の選定は装置設計の核心部分であり、各ポイントはトレードオフの関係になりやすく、バランスの取れた選択が求められます。以下の6つのポイントを考慮して、最適な機構を選定しましょう。
- 動作の効率性
- 精度・耐久性
- コスト
- 製造性
- 拡張性
- メンテナンス性
動作の効率性
動作効率を高めるには、動きの無駄を省き、最短経路で目的の動作を実現する機構を選ぶことがポイントです。直線運動であれば複雑なリンク機構よりもリニアガイドを使用するなど、シンプルな構造を心がけましょう。
動作の加減速を最適化し、振動や衝撃を最小限に抑える機構設計も重要です。「最短距離で目的地に到達する」ようなもので、無駄な動きや複雑さを排除できれば効率向上につながります。
ロボットを例に挙げた場合、動作経路を最適化できればサイクルタイムを短縮できますし、直線運動と回転運動を組み合わせた複雑な動きも実現できます。動作効率の高い機構設計は「無駄を省いたシンプルな動き」を実現するものであり、生産性向上のカギともなるのです。
精度・耐久性
精度と耐久性は相反する要素であることが多く、適切なバランスを見つけることがポイントとなります。高精度を求めると部品のクリアランス(隙間)を小さくしますが、それによって摩耗が早まり耐久性も低下するといったトレードオフになりやすいです。
この点においては、実際に求める精度のレベルを見極め、過剰スペックを避けるように工夫しましょう。例えば、±0.01mmの精度を要する場合と±0.1mmの精度で十分な場合では、選ぶべき機構や部品が異なります。
使用環境や運転時間も考慮して、適切な耐久性を確保してください。バランスにおいては「必要十分な性能」を見極めることが重要ですので、過剰な性能を求めずに実用的な設計を行ってください。
コスト
コスト効率の良い機構設計では、必要十分な機能を持ちながら過剰な要素を省いた設計がポイントです。高価な特注部品よりも標準部品を活用したり、複雑な機構よりもシンプルな機構で同じ機能を実現したりできれば、コストを抑えることができます。
コスト評価では、失敗しないためにも以下の要因を総合的に考えてください。
- 初期コスト(設計・製造コスト)
- メンテナンスコスト(部品交換、点検費用)
- 運用コスト(電力消費、消耗品)
ライフサイクルコストで判断できれば、初期コストが安くても、運用コストが高い機構となるリスクも避けられます。コスト効率の良い機構選定は「必要な機能を適正価格で実現する」ことであり、短期的なコストだけでなく長期的な視点での評価が大切です。
製造性
製造しやすい機構設計では、加工方法や組み立て手順を考慮して部品形状を工夫するのがポイントです。複雑な形状よりも単純な形状、特殊な加工よりも一般的な加工方法を選ぶことだけで、製造のしやすさと品質の安定性を高められます。
例えば、複数の部品を一体化できれば組み立て工程を省略できますし、対称形状であれば組み立てミスを防止できます。
- 部品点数の削減(組み立て工数の削減)
- 標準部品の活用(調達の容易さ)
- 組み立て方向の統一(作業効率の向上)
などは、特にチェックしておきたい点です。製造性の高い設計は「同じ結果をより簡単な手順で達成する」ことを目指すものであり、生産現場の視点を取り入れた実用的な設計を心がけてください。
拡張性
将来の拡張性を考慮した機構設計では、生産量の増加や製品バリエーションの追加に対応できる柔軟性を持たせることがポイントとなります。モジュール化した構造にしたり、余裕を持った設計にしたりできれば、将来の変更に柔軟に対応できます。
例えば、制御システムも将来の機能追加を見据えた余裕のある設計にすると、ソフトウェアの更新だけで新機能を追加可能です。装置のフレーム構造に余裕を持たせることで、あとから新しいユニットを追加するといったこともできます。
拡張性の高い設計は「将来のニーズ変化に対応できる余裕」を持たせることができ、装置の長期的な価値を高めることにもつながります。
メンテナンス性
メンテナンス性の良し悪しは、装置のダウンタイム(停止時間)に直結します。だからこそ、メンテナンスのしやすさを設計段階で考えることで、保守作業の効率化と装置の稼働率向上を狙うのがポイントです。
メンテナンス性を高めるためにできることは、以下が挙げられます。
- 交換頻度の高い部品ほど、アクセスしやすい位置に配置する
- 配線や配管も整理して配置し、点検時に識別しやすくする
- 制御プログラムにエラーログ機能を実装し、トラブルの履歴を残す
メンテナンス性の高い設計は「将来の手間を省く投資」であり、長期的な視点で装置の価値を高めるものです。例えば、点検口を適切に配置できると分解作業を最小限に抑えた点検が可能になりますし、消耗部品のユニット化は交換作業の時間短縮につながります。
装置の設計でよくある失敗事例
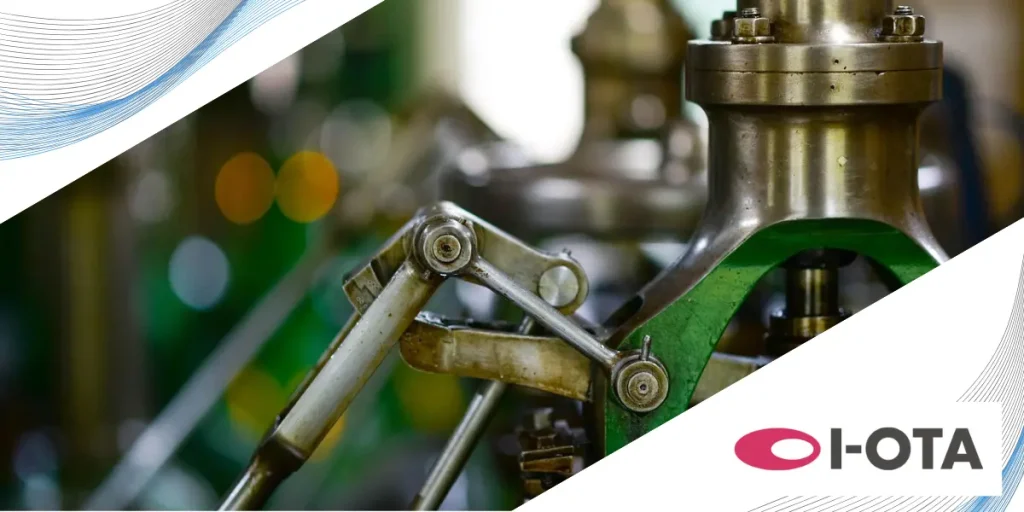
装置設計では、経験不足や検討不足によって以下の問題が発生します。
- 要件定義の不備
- 機構選定ミス
- コスト超過
- 納期遅延
要件定義の不備
要件定義の不備は、完成した装置が期待通りに機能しない主要な原因の1つです。「処理能力が不足している」「想定外の製品バリエーションに対応できない」といった問題が典型的な例でしょう。
要件定義の不備を防ぐためには、要件収集の段階で関係者全員を巻き込み、将来の変化も想定した余裕のある要件定義を行うことがポイントです。
現在の生産量だけでなく、将来の増産計画も考慮した処理能力を設定できれば、装置の長期的な有用性を確保できます。「明確で具体的な目標設定」と「関係者間の共通理解」を重視・徹底し、後工程での問題を回避しましょう。
機構選定ミス
機構選定のミスは、装置の性能不足や頻繁な故障を引き起こす原因となります。設計した装置で、「想定よりも早く部品が摩耗してしまう」「精度が出ない」といった問題に直面したことはないでしょうか。
機構選定ミスの典型的な例としては、以下のようなものが挙げられます。
- 負荷に対して強度が不足する
- 精度要求を満たせない
- 耐久性が不足する
この問題を防ぐためには、設計段階での十分なシミュレーションや、類似事例の調査、専門家の意見聴取などを行うことが有効ですです。過去の経験や成功事例を参考にしつつ、新しい技術も積極的に取り入れることで、最適な機構選定が可能になります。
コスト超過
コスト超過は、どのようなプロジェクトであっても頻繁に発生する問題です。例えば、「想定外の特注部品が必要になる」「設計変更による追加コスト」といった事態が発生します。
コスト超過を防ぐためには、設計初期段階でのコスト試算、標準部品の積極活用、設計変更の影響範囲を最小化する構造などが効果的です。設計の早い段階で部品表(BOM)を作成し、コストの大部分を占める主要部品を特定するだけでも、コスト管理の焦点を絞ることができます。
コスト超過を防ぐには「早期のコスト把握」と「変更に強い設計」が重要であり、予想外の出費を最小限に抑えるための計画と工夫がポイントになります。
納期遅延
納期遅延は、製品だけに限らず顧客満足度に直結する問題です。「設計変更の連鎖」「部品調達の遅れ」「試運転での予想外の問題」などが典型的な原因です。
- 余裕を持ったスケジュール設定
- マイルストーンの明確化
- リスクの早期特定と対応
などに加え、クリティカルパス(全体の納期に直接影響する作業の流れ)を特定し、重点的にリソースを配分して全体の納期リスクを低減しましょう。
部品調達のリードタイムを考慮した設計を行い、トラブルシューティングの時間をあらかじめスケジュールに組み込んでおくなど、各ステップの所要時間を正確に把握し、遅延の連鎖を防ぐことが肝要です。
装置の設計では目的・要件の明確化が課題
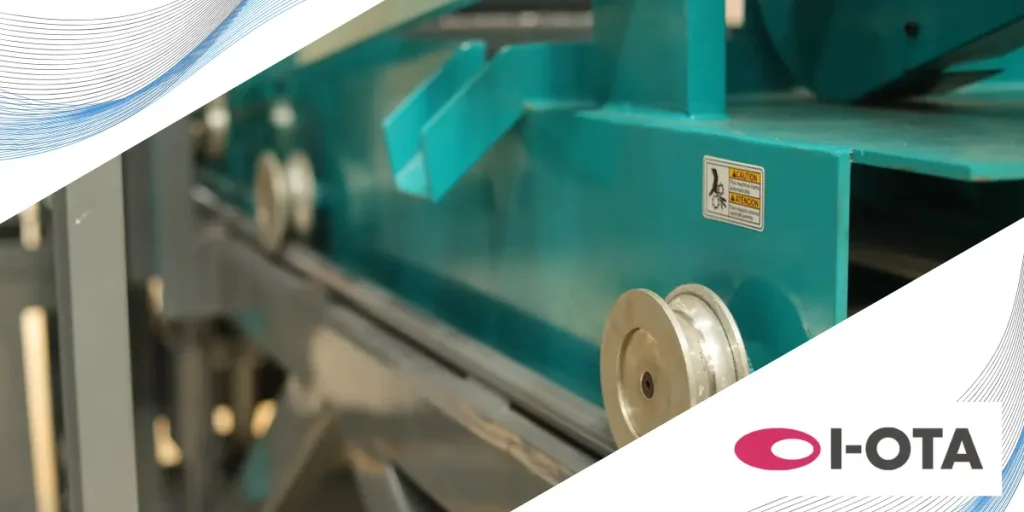
ここまで装置の設計におけるポイントをお伝えしましたが、何をするにしても根幹として用意しなければならないのが「なぜこの装置が必要なのか」という目的の明確化です。家を建てる前に設計図が必要なように、装置も明確な目的がなければ軸を置いた設計はできません。
まず、現状の問題点や課題を洗い出すことからはじめましょう。「不良率を現状の5%から1%以下に削減する」「生産能力を1.5倍に向上する」「作業者の負担を軽減し、安全性を高める」といった具体的な目標を設定できれば軸も見えてきます。
装置設計でお困りならI-OTAへ
- 「どのような装置が最適か判断できない」
- 「課題を発見する・設計を行うリソースが社内にない」
- 「過去の失敗を繰り返したくない」
といった課題をお持ちではないでしょうか。
I-OTAは、日本トップクラスの技術と経験を有した製造業の知見を活かし、お客様の課題をワンストップで解決できる大田区を拠点としたモノづくりのプロ集団です。製品企画から試作品開発、設計、加工まで一貫して対応可能です。
実際に対話をしながら最適な製品や装置を作り上げる「共創」のアプローチで、ご要望を丁寧にヒアリングし、現場の知見と最新のデジタル技術を融合した解決策を提案します。装置設計でお悩みの際は、ぜひI-OTAにご相談ください。
まとめ
装置設計は製造業の要となる工程であり、しっかりとした計画と実行が必要です。予算、スケジュール、ユーティリティなどの制約条件を理解し、そのなかで最適な設計を目指しましょう。
装置構成の決定では、全体の分割方法、部品の送り方、供給方法、加工方法を検討し、効率的な生産体制を構築することが大切です。機構選定では動作効率性、精度、コスト、製造性、拡張性、メンテナンス性のバランスを考慮して、長期的な視点での選択がポイントです。
I-OTAでは、装置設計のプロとして、お客様の課題解決をサポートします。製品企画から試作開発、設計、加工まで一貫して対応可能な体制で、お客様と共に最適な装置を作り上げます。装置設計でお悩みの際は、ぜひI-OTAにご相談ください。
よくある質問(FAQ)
機械設計に必要な知識は?
機械設計には、力学(静力学、動力学、材料力学、流体力学)の4つの基礎知識が必要です。静力学は力のつり合いを、動力学は物体の運動と力の関係を、材料力学は材料の強度や変形を、流体力学は液体や気体の流れを理解するための学問です。
また、CADなどの設計ツールの操作スキルや、製図規格(JIS等)の知識も実務では必須となります。電気制御の基礎知識やコスト計算の知識があると、より良い設計が可能になります。
機械設計の4大力学とは?
機械設計の基礎となる4大力学は以下のとおりです。
力学の種類 | 内容 | 設計での活用例 |
---|---|---|
静力学 | 力のつり合いや構造物の安定性 | フレーム構造の設計、支持部の強度計算 |
動力学 | 物体の運動と力の関係 | 機構の動作設計、振動解析 |
材料力学 | 材料の強度や変形 | 部品の肉厚決定、強度計算 |
流体力学 | 液体や気体の流れ | ポンプ設計、冷却システム設計 |
この4大力学は機械設計の「四本柱」であり、機械を設計するための基礎となります。実際の設計では、この力学を組み合わせて活用することが多く、総合的な理解が求められます。
機械設計の3つのプロセスは?
機械設計の3つの基本プロセスは、「構想設計」「基本設計」「詳細設計」です。
プロセス | 内容 | 成果物 |
---|---|---|
構想設計 | 装置の基本コンセプトや動作原理、全体構成を決定 | 概念図、基本レイアウト |
基本設計 | 主要部品の配置や寸法、動作シーケンスなどを具体化 | 基本図面、主要部品リスト |
詳細設計 | 個々の部品の材料、寸法、公差などを細かく決定 | 詳細図面、部品表、製造指示書 |
上記の3つのプロセスは「粗い設計から細かい設計へ」と段階的に詳細化していく流れになっています。構想設計では大きな方向性を決め、基本設計でその骨格を形作り、詳細設計で具体的な製造情報を完成させるといった具合です。
設計に必要な能力は?
設計に必要な能力は、以下のとおりです。
- 論理的思考力
- 創造力
- コミュニケーション能力
- 問題解決能力
設計能力と一言にいっても、いわゆる「パズルを解く力」と「物語を創る力」の両方を持ち合わせた、バランスの取れた思考能力が求められます。この能力は、経験を通じて徐々に磨かれていくものであり、継続的な学習と実践を繰り返しましょう。
機械設計のステップは?
機械設計の基本的なステップは以下のとおりです。
- 要件定義
- 構想設計
- 基本設計
- 詳細設計
- 検証
機械設計は「抽象から具体へ」と段階的に進む過程です。順序立てて進めることで、高品質な設計が可能になります。各ステップの終了時にはレビューを行い、次のステップに進む前に問題点を解決しましょう。