製品開発において、アイデアを形にする「試作製造」は失敗を減らすためのプロセスです。しかし、「試作と量産の違いは何か」「どのような段階を踏むべきか」といった疑問を持つ方も多いのではないでしょうか。
本記事では、試作製造の基本概念から試作・量産への移行を成功させるためのノウハウや、よくある失敗事例まで解説します。製品開発に携わるエンジニアや新規事業を立ち上げようとしている経営者・起業家の方は、製品開発の参考にしてください。
試作製造とは?
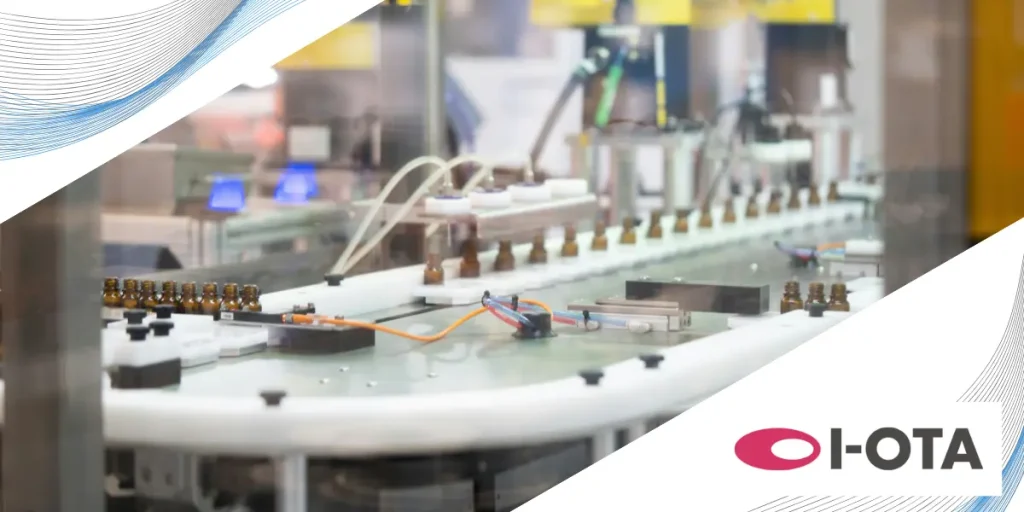
試作製造とは、製品を本格的に製造販売する前に、試験的に作ってみるプロセスのことです。品質、機能、デザイン形状、コストなどを確認するために実際にサンプル製品(プロトタイプ)を作る工程です。
試作製造では、実際に動作する試作機を何度も作って検証することで、製品の完成度を高めていきます。試作は段階を踏んで何度も製作し、各段階の問題をクリアしてはじめて量産品の製造を開始できます。
試作は「形になるか?」の初期段階から「すべての問題がクリアできているか?」の最終確認まで、製品化へのステップとなるのです。
試作と量産の違い
試作と量産の違いは、主に生産方法にあります。
試作は少量生産に適した方法で作られ、主に3Dプリンター、切削加工、真空注型などの少量生産に適した方法で製造します。一方、量産は大量生産に適した方法で作られます。量産品はほとんどが金型を使った射出成形という方法で大量生産します。
わかりやすく言い換えると、試作は「特注品を作る」工程で、量産は「同じものを効率よく大量に作る」工程だということです。「アイデアを形にする」のが試作で、「大量生産できるか確認する」のが量産試作となります。
試作製造の4つの段階
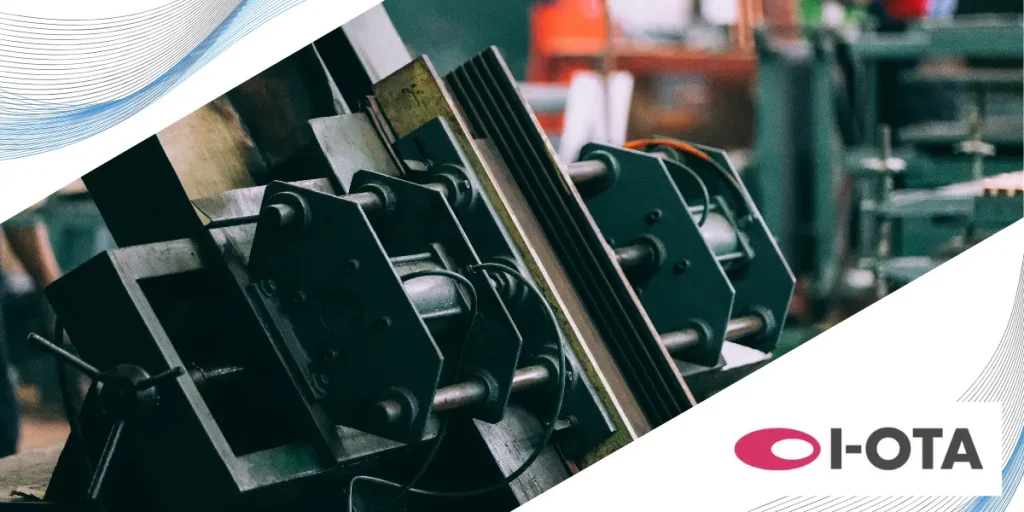
試作製造は、一般的に以下の4つの段階にわけられます。
- 原理試作
- 機能試作
- デザイン試作
- 量産試作
原理試作
原理試作は、製品の機能や性能を限定して実際に形にする最初の段階です。この段階では「この製品は作る価値があるか?」という製品コンセプトの実証(Proof of Concept/PoC)を行います。
「そもそもこのアイデアは実現可能か?」を確かめるための試作で、動作しない外見だけのモデル(コールドモック)の場合もあります。例えるなら、新しい自転車のアイデアがあるとき、まず段ボールで大まかな形を作ってみるようなイメージです。
機能試作
機能試作は、製品が仕様通りに動くかを検証する「技術検証段階」です。原理試作でできた試作品に機能を足して、実際に動作するか確認します。
機能試作は通常、3つの段階的なステップで検証を進め、製品の完成度を高めていきます。
- EVT1:「とりあえず動くか」を確認する
- EVT2:ちゃんと動くように改良する
- EVT3:完成形に近づける
大まかに段ボールで作った自転車の形に、実際にペダルやハンドルの機構を取り付けて動くか試すようなイメージです。機能試作では、細かい調整ができるのでさまざまなチャレンジが可能です。「理論上できるはず」から「実際に動く」への橋渡しをする段階だといえます。
デザイン試作
デザイン試作は、機能試作で検証された製品に好ましい外観を付ける段階です。市場ニーズや使いやすさを考慮したデザインを検討します。インダストリアル・プロダクトデザインとも呼ばれます。
先の例でいえば、動く自転車のメカニズムができたら、見た目を格好良くしたり、乗りやすくしたりする段階です。3Dプリンターの活用も進み、自由度は上がってきています。機能だけでなく「使う人」を意識した製品の形を決める段階となります。
量産試作
量産試作(PP:PreProduction)は、原理試作、機能試作、デザイン試作を反映した量産を実現するための試作です。量産品に採用する製品設計で、少量生産して検証します。
最後に、自転車工場で使う材料や部品、製造ラインを使って少数の自転車を試作するといった具合です。量産試作は、DVT(設計検証試験)とPVT(生産検証試験)という2つの段階に分かれます。
- DVT(設計検証試験):製品の設計が仕様通りに機能するかを検証する
- PVT(生産検証試験):実際の量産プロセスを検証する
簡単にまとめると、「本番と同じ条件で少し作ってみる」段階で、量産への最終関門となります。
試作製造の5つの主な加工方法
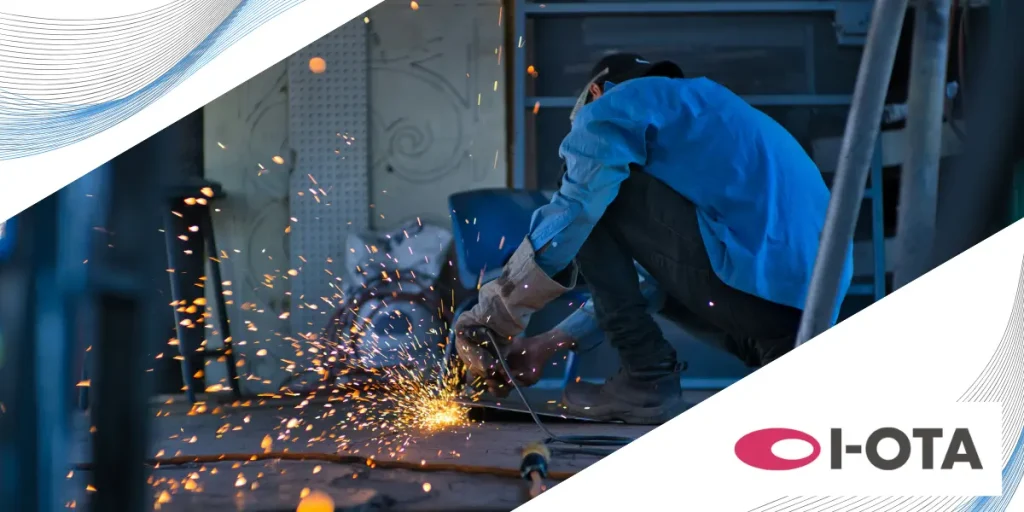
試作製造には、目的や段階に応じて以下のようなさまざまな加工方法があります。
- 簡易型の射出成形
- 切削加工
- 真空注型
- 3Dプリンター
- レーザー加工・エッチング
簡易型の射出成形
簡易型の射出成形は、樹脂型やアルミ型、カセット型など比較的安価な金型を使う方法です。本型(量産用金型)より安価で作れますが、ショット可能数が少なく型の寿命も短いという特徴があります。
例えるなら、本格的な鉄の型を作る代わりに、アルミや樹脂で型を作るようなイメージです。量産品にもっとも近い試作品に適した製法で、量産と同じ材料で作ることが可能です。「本番に近い条件で少量だけ作る」ための方法で、量産前の最終確認に適しています。
切削加工
切削加工は材料のブロックを削って成形する方法で、精度が高く丈夫な試作品ができます。量産とほぼ同じ材料が使えるのがメリットですが、コストが高くなるのがデメリットです。
素材から余分な部分を削り取って形を作り出すといった具合で、1つひとつ削って製作するため、数量が多いほどコストがかかります。「数個単位で精度の高い試作品」を作りたい場合に向いている製法です。
真空注型
真空注型は、真空状態でゴム型に液体状の樹脂を流して固める製法です。1つの型で20個ほどのコピーが作れ、少量生産に適しています。
- ウレタン系
- エポキシ系
- シリコン系
などの素材に限られますが、特殊技術ではナイロン6といった注型を使うことも可能です。「オリジナルを少数コピーする」のに適した方法で、少量の評価用サンプルを作るのに向いています。
3Dプリンター
3Dプリンターは、3Dデータから直接立体物を積層造形する製造装置です。通常のプリンターが紙に平面印刷するのに対し、3Dプリンターは空間に立体的に「印刷」します。
データからすぐに造形できるため、開発期間の短縮とコスト削減が可能です。複数の造形方式があり、それぞれに特徴があります。デザイン検討や形状確認に最適なツールで、「データから直接形にする」という新しいものづくりの手法を実現しています。
レーザー加工・エッチング
レーザー加工やエッチングは、薄い板材から部品を切り出す金型レス加工方法です。初期費用を抑えて短納期で作れるため、原理試作に適しています。
紙をハサミで切り抜くように、レーザーや化学薬品で金属や樹脂の板から形を切り出すといった具合です。薄板プレス部品の試作では、抜き(ブランク)部の加工に用いられます。「薄い材料から形を切り出す」方法で、電子部品や精密部品の試作に向いています。
試作から量産への移行を成功させるための3つのポイント
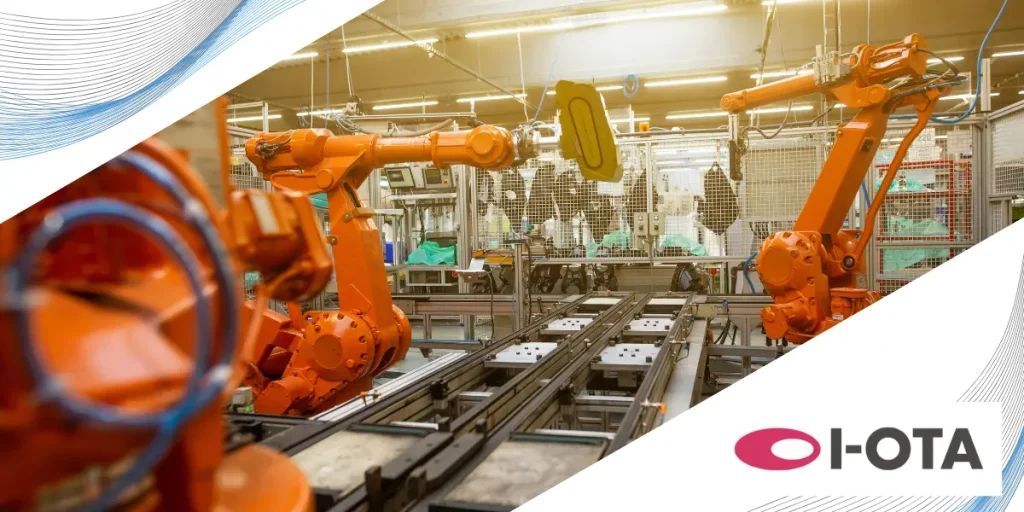
試作から量産への移行を成功させるためには、以下の3つのポイントが重要です。
- 量産を見据えた設計変更は早い段階に行う
- 初期費用・製造コストのバランスを取る
- 試作と量産での品質差を最小化する
量産を見据えた設計変更は早い段階に行う
試作から量産への移行を成功させる1つ目のポイントは、量産を見据えた設計変更をできるだけ早い段階で行うことです。試作の段階が進むほど、設計変更のコストと時間が増大するからです。
家の設計図の段階で変更するのは簡単ですが、基礎工事がはじまってからの変更は大変なように、製品開発も同じ苦労を抱えかねません。金型設計に関わる変更は、量産直前では対応が難しく高コストになります。そのためにも、「作れるか」だけでなく「量産できるか」の視点を早い段階から持つことが重要です。
初期費用・製造コストのバランスを取る
試作から量産への移行を成功させる2つ目のポイントは、コスト計画において、初期費用(設計費、試作費、金型費など)と製造コスト(材料費、加工費など)のバランスを取ることです。
基本となる計算式は、「販売予想数」(売上)-「初期費用」-「材料費」=「利益」です。例えば、100円で売りたい商品なら、初期費用100万円、材料費50円/個の場合、5万個以上売らないと利益が出ない計算になります。
コストを意識しないで設計を進めると、量産段階で「コストが高すぎる」という問題に直面します。製品開発の初期段階からコスト意識を持ち、採算が取れる製品設計を目指すことが大切です。
試作と量産での品質差を最小化する
試作から量産への移行を成功させる3つ目のポイントは、試作と量産では製造方法が異なるため生じる品質の差を最小化することです。量産前の試作段階で、量産と同等の品質を確保するための検証が重要です。
例えば、手作りのケーキと機械で大量生産するケーキの味や見た目の差を最小限に抑えるようなイメージです。重要な機能や性能については、量産条件に近い環境での試験評価が必要です。試作段階で「量産でも同じ品質が出せるか」を常に意識し、対策を講じることが成功の鍵となります。
試作製造における5つの失敗事例
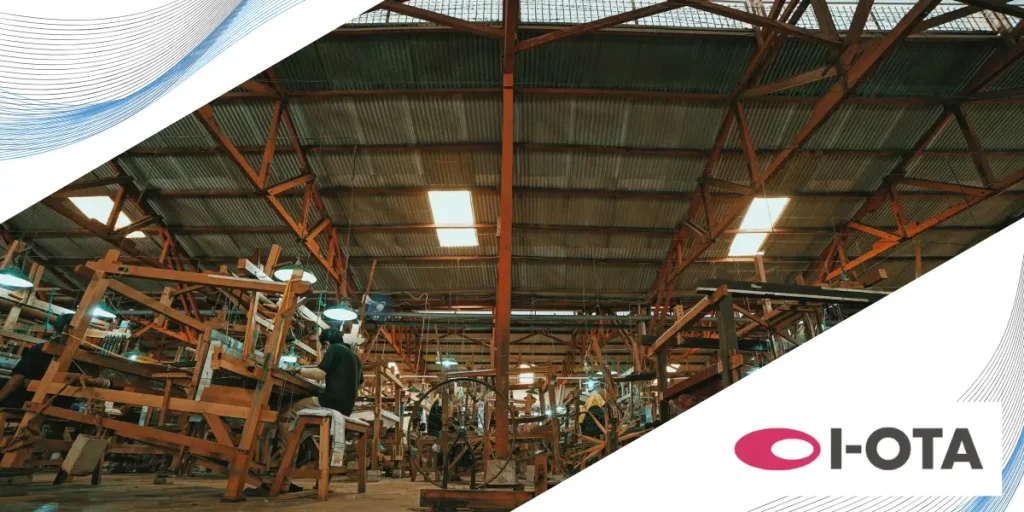
試作製造から量産への移行では、さまざまな失敗事例があります。
- 量産できない形状設計となってしまった
- コスト計算の甘さで予算をオーバーした
- 材料選定ミスで性能不足になった
- 試作段階での検証不足が品質問題を招いた
- 量産工程を考慮しない製造方法を選んだ
量産できない形状設計となってしまった
試作製造における1つ目の失敗事例は、3Dプリンターなどでは作れても、金型では抜けないような複雑な形状を設計してしまうケースです。3Dプリンターは金型が不要で、データがあれば造形できますが、量産では型が必要になります。
アンダーカット(型から取り出せない形状)や極端に薄い壁、深すぎる穴などが量産の障害になります。対策としては、初めの設計時点から金型を意識した設計(DFM:Design for Manufacturing)を心がけることです。「作れる形」と「量産できる形」は異なるため、量産を見据えた形状設計を考えましょう。
コスト計算の甘さで予算をオーバーした
試作製造における2つ目の失敗事例は、試作段階ではコストを十分に考慮せず、量産段階で予算を超えてしまうケースです。クラウドファンディングで資金調達をした後、いざ量産に取り掛かると調達額を大きくオーバーしてしまうような状況がこれにあたります。
市場に出回っている安価な製品と同じ価格帯を目指すと、大量生産が前提となるため個人や小規模事業では難しいことがあります。初期段階から詳細なコスト計算を行い、現実的な販売価格と生産数を設定することが重要です。「売れる価格」と「作れる価格」のバランスを取ることを忘れないようにしましょう。
材料選定ミスで性能不足になった
試作製造における3つ目の失敗事例は、試作と量産で異なる材料を使用することによる性能差が生じるケースです。試作では高性能な特殊材料を使ったが、量産ではコスト面から一般的な材料に変更したら性能が出なくなったというのはよくある失敗です。
素材選定でミスが発生してしまえば、強度、耐熱性、耐久性などの物理的特性や、色、質感などの外観特性に差が出やすくなります。試作段階から量産で使用する予定の材料を使うか、少なくとも同等の特性を持つ材料で評価するのがポイントです。だからこそ、「試作で使う材料」と「量産で使う材料」の違いを理解し、適切な材料選定を行うことが重要です。
試作段階での検証不足が品質問題を招いた
試作製造における4つ目の失敗事例は、試作段階で十分な検証を行わず、量産後に品質問題が発覚するケースです。短期間の使用テストだけで耐久性を判断し、長期使用で不具合が発生するような状況です。
主に、環境試験(温度、湿度、振動など)や耐久試験、ユーザビリティテストなどが不足しやすくなります。対策としては、試作段階で想定される使用条件や極端条件での十分な検証を行うことが挙げられます。「動けばOK」ではなく、「あらゆる条件で安定して動くか」を検証しましょう。
量産工程を考慮しない製造方法を選んだ
試作製造における5つ目の失敗事例は、試作段階の製造方法が量産に適さず、製造工程の変更が必要になるケースです。手作業で組み立てていた試作品を自動化ラインで生産しようとしたら、設計変更になったというような状況が当てはまります。
このケースでは、組み立て性、検査性、メンテナンス性など、量産工程を考慮していない設計が問題になります。この点においては、設計段階から製造エンジニアを巻き込み、量産性を考慮した設計(DFA:Design for Assembly)を行うことが重要です。「作る」だけでなく「効率よく作れるか」の視点を持ちましょう。
少量生産・高付加価値化の新たなビジネスモデル
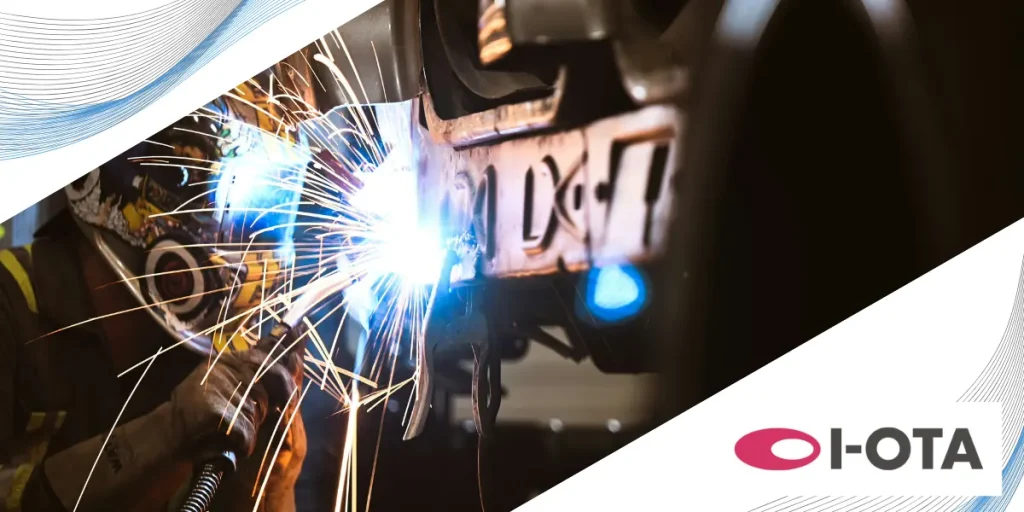
近年では、大量生産・大量消費だけでなく、少量生産で高付加価値を持つビジネスモデルも注目されています。大量の在庫を抱えずに、多種多様な顧客ニーズに対応できるようになってきたからです。
例えば、100円の大量生産品と競争するのではなく、1,000円でも欲しいと思わせる価値を持つ製品を作るといった具合です。消費者は、性能や品質など同等の製品なら安い方を選びますが、高付加価値のある製品ならそのニーズを必要としている人は価格が高くても購入します。
であるからこそ、「たくさん作って安く売る」だけでなく「少量でも価値があるものを適正価格で売る」という選択肢も考慮すべきでしょう。試作製造の技術を活かした少量多品種生産は、このようなビジネスモデルと相性が良いといえます。
試作製造の外部委託先選びにおける4つの基準
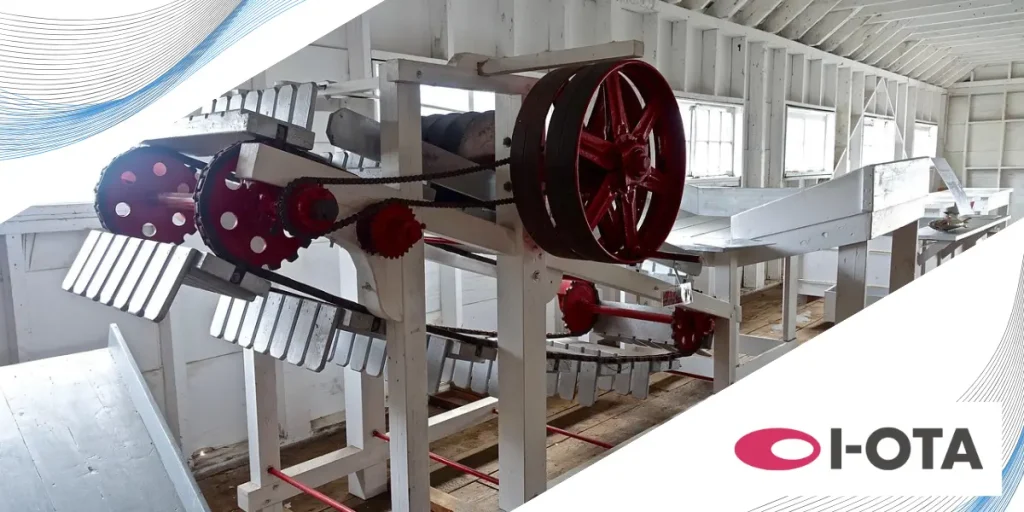
試作製造を外部に委託する際には、以下の4つの基準で選ぶことが重要です。
- 目的に合った加工能力を持っているか
- 設計変更にも迅速に対応できるか
- 密な情報共有ができる関係性となれるか
- 安心して任せられるか
目的に合った加工能力を持っているか
試作の目的や要求仕様に合わせた技術力と設備を持つパートナーを選ぶことが重要です。パートナー企業の得意分野や保有設備を事前に確認することで、最適な試作方法を選択できるからです。
精密な金属部品の試作なら高精度な切削加工機を持つ会社、樹脂部品なら3Dプリンターや射出成形の設備がある会社など、製品に合わせた選択が必要です。特殊な材料や加工方法が必要な場合は、その分野に特化した専門企業を探すことをおすすめします。
「何を作りたいか」に合わせて「どのような技術・設備を持つパートナーが適切か」を判断することがポイントです。企業のWebサイトや過去の実績を見ると、その企業の加工能力を判断できるでしょう。
設計変更にも迅速に対応できるか
試作段階では設計変更が頻繁に発生するため、迅速かつ柔軟に対応できるパートナーが理想的です。例えるなら、「この部分をもう少し薄くしたい」「ここの角度を変えたい」といった要望に素早く対応できる体制があるかということです。
短納期対応力や、急な仕様変更への対応力は、開発スピードにも直結します。開発初期段階では、試行錯誤を繰り返すことが多いため、柔軟な姿勢のパートナーが望ましいでしょう。過去の対応実績や、初回の問い合わせへの対応スピードを見ると判断しやすくなります。
密な情報共有ができる関係性となれるか
試作製造では、技術的な課題や改善点について密なコミュニケーションが取れるパートナーが長期的な視点で重要です。依頼を受けて作るだけでは、良いものに仕上がらないからです。
単に発注通りに作るだけでなく、製造のプロとして適切なアドバイスをくれるパートナーが理想的です。例えば、「この形状は量産が難しいので、こう変更してはどうか」といった提案をしてくれるような関係性が望ましいでしょう。初回の打ち合わせでの質問内容や提案内容を見ると、コミュニケーション能力や提案力を判断できるはずです。
安心して任せられるか
パートナー選びでは、過去の実績や顧客評価、業界での信頼性を確認することもポイントです。
- 類似製品の試作実績があるか
- 品質管理体制は整っているか
- 納期は守られているか
などの点をチェックしましょう。可能であれば、実際の製造現場や設備を見学したり、サンプル品を確認したりすることも有効です。「技術力があるだけ」ではなく「安心して任せられる」パートナーを選ぶことが長期的な成功につながります。企業の設立年数や取引実績、品質管理の認証取得状況なども見ておくと、信頼性を判断できるでしょう。
試作の製造請負先はワンストップ対応のI-OTAへ
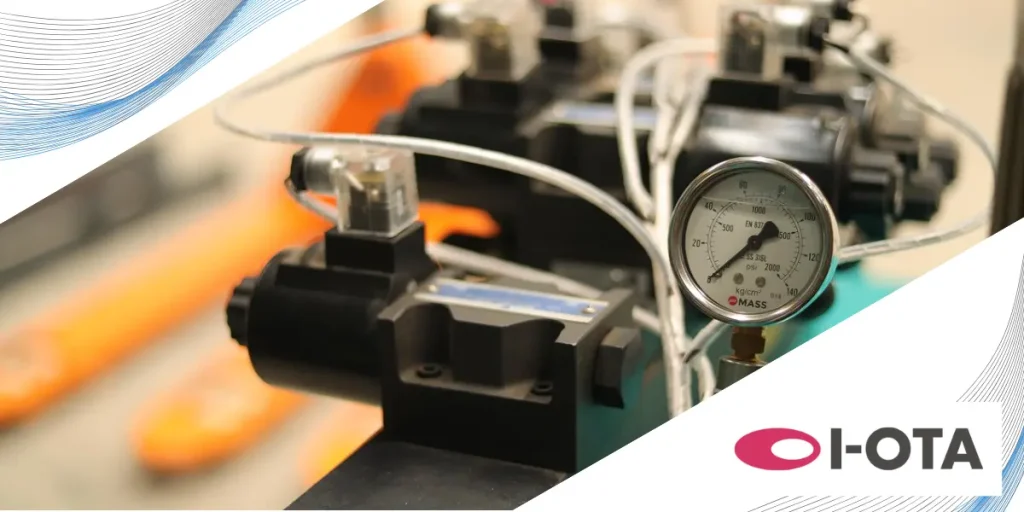
製品開発の試作製造をお考えなら、大田区発の共同事業体I-OTAへお任せください。製品企画から試作品開発、設計、加工までをワンストップで対応できる体制を整えています。
I-OTAの特徴は、モノづくり経験豊富な現場力とDXを融合した連携にあります。すでに図面をお持ちのお客様はもちろん、アイデア段階からの相談も可能です。金属加工、樹脂加工、表面処理など幅広い技術・経験を持った企業が参画しているため、さまざまな試作ニーズに対応できます。
お客様の課題に合わせて最適なプロジェクトチームを編成し、設計開発・製造・各種検査・実証実験まで一貫してサポートします。試作から量産化までの道のりをスムーズに進めるパートナーとして、ぜひI-OTAにご相談ください。
まとめ
試作製造とは製品の量産前に少量で製造し検証するプロセスで、目的別に原理試作・機能試作・デザイン試作・量産試作の4種類があります。試作と量産では製造方法が異なり、試作は少量生産に適した方法、量産は大量生産に適した方法を用います。
試作から量産への移行を成功させるためには、早い段階での設計変更、コストバランスの考慮、品質差の最小化がポイントとなります。I-OTAでは、お客様の課題に合わせて最適なプロジェクトチームを編成し、設計開発・製造・各種検査・実証実験まで一貫してサポートします。
試作から量産化までの道のりをスムーズに進めるパートナーとして、ぜひI-OTAにご相談ください。
よくある質問(FAQ)
試作作業とは何ですか?
試作作業とは、製品の設計図やアイデアを実際に形にする作業のことです。3Dプリンター、切削加工、真空注型、簡易金型などさまざまな方法で試作品を製作します。
試作作業には、設計データの作成、材料選定、加工方法の選択、実際の製作、検査・評価などの工程が含まれます。「頭の中のアイデア」や「画面上の設計」を「実際に触れるもの」に変換する一連の作業です。
DVTとPVTの違いは?
DVTは「製品自体の検証」、PVTは「製造プロセスの検証」という違いがあります。
- DVT(Design Verification Test/設計検証試験):製品が設計通りにできているかを検証
- PVT(Process Verification Test/生産検証試験):製品が大量生産に適した設計になっているかを検証
例えるなら、DVTは「設計図通りに家が建てられたか」を確認し、PVTは「同じ家を何百棟も効率よく建てられるか」を確認するようなものです。両方のテストを経てはじめて、製品は本格的な量産に移行できます。
原理試作と機能試作の違いは?
原理試作と機能試作は、製品開発プロセスにおける異なる段階の試作を指します。原理試作が「このアイデアは実現できるか」を確かめる段階なのに対し、機能試作は「このアイデアを製品として実装できるか」を検証する段階だといえます。
原理試作(Proof of Concept Prototype)は、製品の基本的なアイデアや原理が実現可能かを確認するための最初の試作です。この段階では、製品のすべての機能を実装する必要はなく、核となる技術や機能が動作するかを検証することが目的です。外観や使い勝手よりも、「そもそもこの製品は技術的に実現可能か」という点に焦点を当てます。
一方、機能試作(Functional Prototype)は、製品の主要な機能が設計通りに動作するかを検証するための試作です。原理試作で確認した基本原理をベースに、より実際の製品に近い形で機能を実装し、性能や信頼性を評価します。この段階では、製品の各機能が個別に動作するだけでなく、それらが統合されたシステムとして正しく機能するかを確認します。