- 製品の設計から製造まで、複数の業者とのやり取りに時間がかかりすぎる
- 工程ごとの予算管理が煩雑で、コストが見えにくい
- 品質管理の基準が業者によってバラバラで、統一が難しい
などの課題を抱えているのではないでしょうか。
近年は、製品開発のスピード化や品質要求の高度化により、従来の分業型製造では対応が困難になってきています。各工程で発生する調整や修正のたびに関係者間での連絡や承認を要し、貴重な時間とコストは失われます。
この状況を改善する有効な手段として注目されているのが「製造業のワンストップサービス」です。設計から製造、品質管理まで一括して任せられるこのサービスは、製造プロセスの効率化とコスト削減を実現する新しい選択肢となっています。
本記事では、製造業におけるワンストップサービスの特徴や5つのメリット、たった1つのデメリットまで詳しく解説します。特に、「製造プロセスの効率化」「コスト削減」「品質管理の統一」にお悩みの方は、ぜひ最後までご一読ください。
製造業の「ワンストップサービス」とは
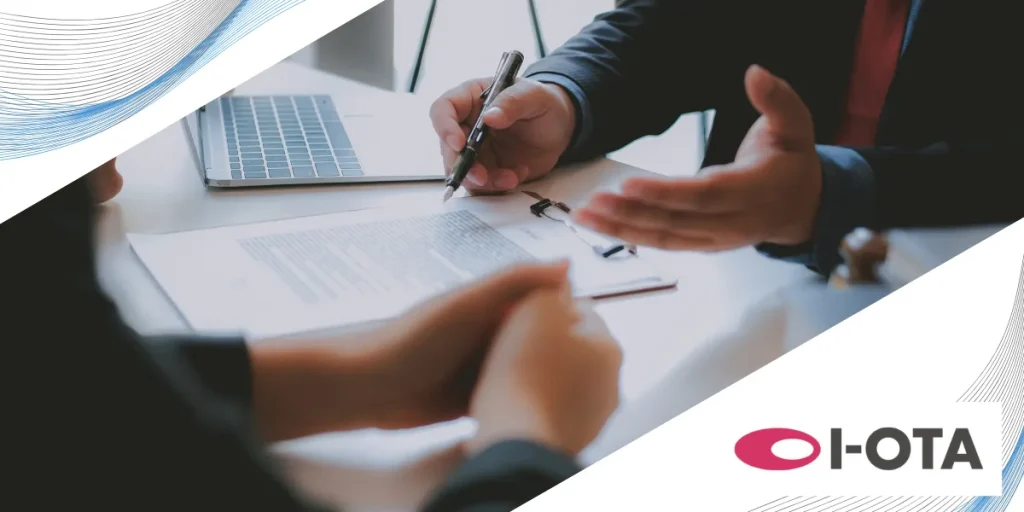
製造業のワンストップサービスとは、製品開発における企画・設計から、部品調達、製造、品質管理、出荷までの全工程を一元的に請け負うサービスのことです。従来は複数の業者に分散していた製造工程を1社で一括して対応でき、効率的な製品開発を実現します。
例えば、新製品の開発では「設計は設計事務所に依頼」「部品は商社から調達」「製造は工場に委託」というように、工程ごとに異なる業者と契約を結ぶ必要がありました。対してワンストップサービスでは、窓口となる1社が全工程の管理・調整を担当。発注側は1社とやり取りするだけで、製品開発のすべてを完結できます。
ワンストップサービスの特徴は、製造工程の『統合』にあります。各工程の専門家やパートナー企業と連携しながら一貫した品質管理とコスト管理を実現し、発注側の手間を削減しつつ高品質な製品開発を目指せるのです。
一貫生産との違い
ワンストップサービスと一貫生産は一見似ているように見えますが、違いは実施主体にあります。
一貫生産は、原材料の調達から最終製品の完成まで、すべての工程を同一組織内で完結させる生産方式です。自社工場で一貫して製造し、品質管理の徹底やコスト削減を図ります。
一方、ワンストップサービスは、各分野の専門企業と連携しながら窓口企業が全体の管理を担当するため、高度な専門性と効率的な生産体制を両立できます。発注側からすれば1社と契約するだけですが、各分野のプロの技術を活用できる点が特徴です。
ODM・OEM・EMSとの違い
ワンストップサービスは、製品開発の『全工程』を包括的に示す概念です。一方、ODM・OEM・EMSは、具体的に「どの範囲を委託できるか」を示す製造形態を表します。
項目 | ODM | OEM | EMS |
---|---|---|---|
サービス範囲 | 設計から製造まで全部 | 製造のみ | 電子機器の製造に特化 |
設計 | ✓ 自社で設計する | × 顧客から設計図をもらう | × 顧客から設計図をもらう |
製造 | ✓ | ✓ | ✓ |
部品調達 | ✓ | ✓ | ✓ |
知的財産権 | 主にODM側 | 顧客側 | 顧客側 |
製品例 | スマホ完成品 | 自動車部品 | スマホの基板 |
このような時に使う | 「このような製品作りたいけど、 設計からお願いしたい」 | 「設計図はあるから、 作るだけお願い」 | 「電子基板の製造を 専門家に任せたい」 |
特徴 | ・企画から製造まで一貫対応 ・顧客の要望を形にできる ・開発期間が必要 | ・製造に特化 ・コスト重視 ・既存設計の量産向き | ・電子機器製造に特化 ・部品調達力が強い ・品質管理が厳格 |
設計から製造まで全部任せたい場合はODM型、製造だけを委託する場合はOEM型、電子機器の製造を専門的に依頼したい場合はEMS型が適しています。ワンストップサービスは、それぞれの形態を包括的に管理する仕組みとして機能します。
製造業のワンストップサービスに依頼できる内容
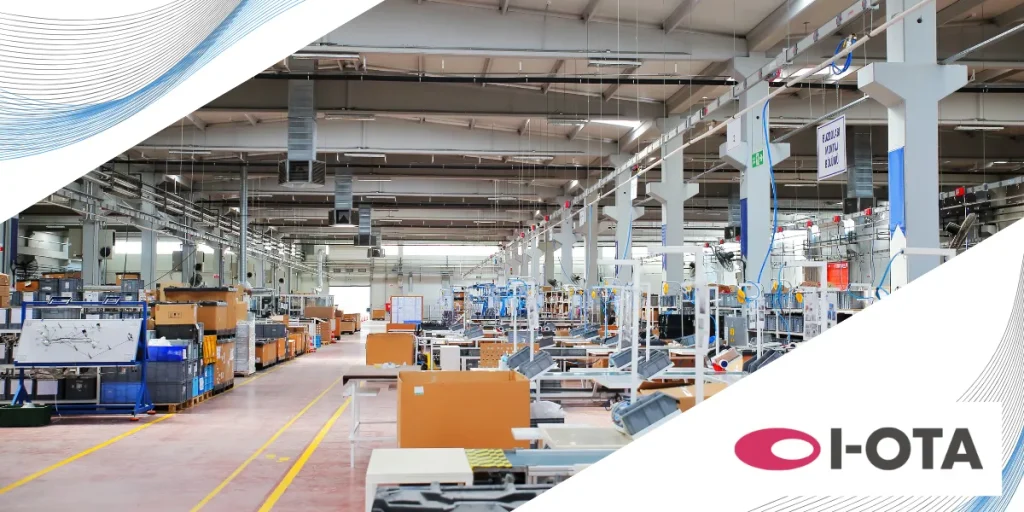
製造業のワンストップサービスに依頼できる内容は、主に以下が挙げられます。
- 製品企画・設計開発
- 試作品製造
- 量産体制の構築
- 品質管理・検査
- アフターフォロー
弊社、I-OTAを例にしているため、実際の内容は各社へ確認を行ってください。
製品企画・設計開発
製造業のワンストップサービスでは、アイデアの段階からの製品開発に対応できます。具体的な図面がなくても、市場ニーズや競合分析を踏まえた製品企画・構想の策定から、詳細な設計図面の作成まで一貫してサポートします。
例えば、「このような製品があったら便利だけど、どう作ればいいかわからない」という段階からでも、技術的な実現可能性の検討や、製造コストを考慮した設計提案を受けることが可能です。
試作品製造
設計図面をもとに、金属加工、樹脂成形、表面処理など、必要な製造工程を最適な技術を持つ協力企業と連携して試作品の製造を行います。
試作過程で発見された課題に対しては、設計へのフィードバックや改善提案を行い、量産を見据えた製造性の向上を図ります。また、製造装置の開発や改良についても、製品品質の安定化や生産効率の向上を目的として提案を受けるといったことも可能です。
量産体制の構築
試作段階で確認された製造方法をベースに、効率的な量産体制を構築します。この際、製造コストの最適化や、品質の安定化、納期管理の効率化などを考慮した生産ラインの設計を行うこともあります。
場合によっては、必要な製造設備の選定や、作業標準の策定、製造スタッフの教育訓練まで含めた包括的なサポートも可能です。
品質管理・検査
製品の品質を保証するため、検査体制の構築もワンストップサービスに含まれる内容の1つです。
製品特性に応じた検査項目の設定や、検査基準の策定、検査装置の導入など、品質管理に関する一連の業務を依頼できます。また、製造工程内での品質チェックポイントの設定や、不良品発生時の対応手順の確立なども含まれます。
アフターフォロー
製品の納品後も、製品の改良提案や、新たな用途開発、市場からのフィードバックに基づく改善活動などの継続的なサポートを受けられます。また、販路開拓のサポートや、製品のメンテナンス体制の構築、補修部品の供給体制の確立なども、必要に応じて依頼できることもあります。
このように、製造業のワンストップサービスでは、製品開発の構想段階から、アフターフォローまでの幅広い業務を一括して依頼可能です。複数の企業との個別調整の手間を省き、効率的な製品開発・製造体制を実現できるのです。
製造業のワンストップサービスの流れ
製造業のワンストップサービスは、以下の4つのステップで進行します。
- 初期相談と課題整理
- 技術者を交えた仕様確定
- 一貫した製造プロセスの実行
- 納品後のフォローアップ
「4つのステップが必要で、手続きが複雑そう…」と感じる方もいるかもしれません。しかし、実際には最初の相談だけで構いません。その後の流れは、ワンストップサービスを提供する企業が主導的にサポートするからです。
I-OTAの場合、お客様の「このような製品を作りたい」という想いから、具体的な製品化までの道筋を示し、実現までしっかりとサポートします。まずは気軽な相談から始めてみてはいかがでしょうか。
製造業のワンストップサービスを使う5つのメリット
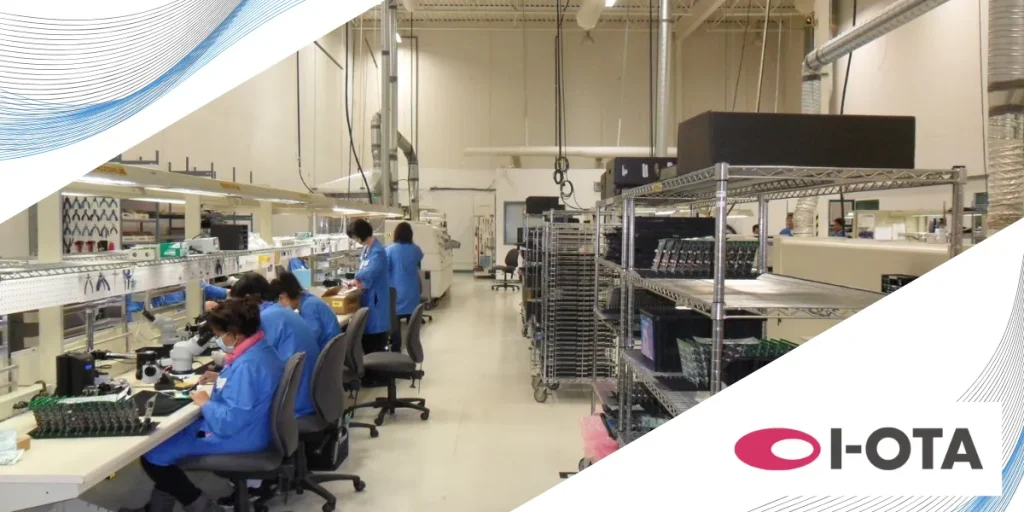
製造業のワンストップサービスを利用すると、以下のメリットが得られます。
- やり取りがスムーズになる
- 予算が分かりやすくなりやすい
- 品質や納期を管理しやすくなる
- 競争力が高まる
- 専門的な提案を受けやすくなる
やり取りがスムーズになる
製造工程を複数の業者に分散させると、それぞれとの打ち合わせや契約手続きに多大な時間と労力がかかっていたはずです。一方で、ワンストップサービスでは、窓口が一本化されることで、煩雑なコミュニケーションが簡素化されます。
例えば、設計変更が必要になった場合でも、1つの窓口を通じて全工程に迅速に情報が伝達され、スムーズな対応が可能になるなどです。また、各工程での進捗状況も一元管理されるため、プロジェクト全体の見通しが立てやすくなります。
予算が分かりやすくなりやすい
従来の分散型製造では、各工程での見積もりや追加費用が個別に発生し、最終的なコストが見えにくい状況でした。ワンストップサービスでは、プロジェクト全体の費用が一括で見積もられるため、予算管理もしやすくなります。
複数の業者への支払い手続きが一本化されることで経理処理の手間も削減でき、一括発注によるスケールメリットをいかしたコスト削減も期待できます。
品質や納期を管理しやすくなる
製造工程が一元管理されることで、品質管理と納期管理が効率化されます。各工程間の連携がスムーズになり、品質上の問題が発生した場合も、原因の特定から対策の実施まで迅速に対応できるからです。
工程間の無駄な待ち時間が削減され、全体の納期短縮にもつながります。一貫した品質基準のもとで製造が行われるため、最終製品の品質安定性も向上するでしょう。
競争力が高まる
ワンストップサービスの導入により、製造プロセス全体の最適化も図れます。結果、コスト削減、納期短縮、品質向上という3つの要素が同時に実現し、市場での競争力が向上します。
急な市場変化や顧客要望への対応が迅速になることで、ビジネスチャンスを逃さず、競合他社との差別化が可能です。
専門的な提案を受けやすくなる
ワンストップサービスでは、参画企業それぞれの専門的な知見を、一貫したフォーマットで受け取れます。従来のように各社からの提案を個別に取りまとめる手間が省け、効率的な意思決定が可能です。
製造工程全体を見渡した総合的な視点からの提案を受けられるため、全体を見通しながら製品改良や工程改善につながります。各分野の専門家の意見が体系的に集約されることで、より質の高い製品開発も実現できます。
製造業のワンストップサービスのデメリット
製造業のワンストップサービスにおけるデメリットは、信頼できるパートナー選定の難しさです。表面的な提案や実績だけでは、自社の製造ニーズに本当に応えられるのか、事前評価が困難だからです。
特に注意が必要なのは以下の3点です。
- 技術力や設備の実態が見えにくい
- 提案の質や深さを事前に判断できない
- 実際の連携体制が不透明
I-OTAでは、まず詳細な無料相談からスタートし、お客様の課題やニーズを丁寧にヒアリングします。
いただいた内容から、昭和時代から受け継がれる確かな技術と大田区の優れた製造業ネットワークをいかし、「できること」「できないこと」を明確にお伝えし、プロジェクトの実現可能性を慎重に見極めます。
ワンストップサービスならI-OTAにお任せください
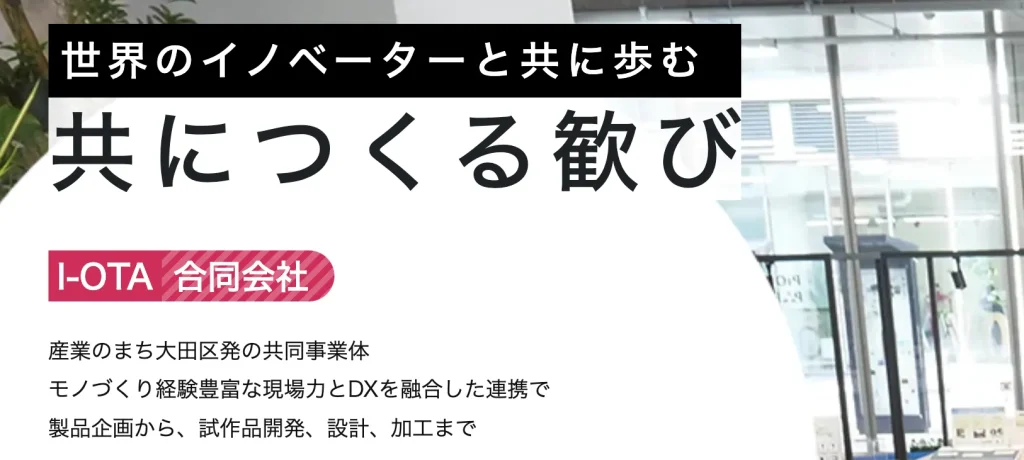
製品開発から製造までの一貫したワンストップサービスをお探しの企業様に、I-OTAがご提案できる強みは「現場力」と「連携力」の融合です。
大田区という日本有数のものづくり集積地で培われた技術基盤と、デジタル技術を組み合わせた新しい製造業のかたちで、お客様の課題に対して、企画・設計から試作、量産まで、一気通貫での解決策をご提供します。
3,500社を超える製造業が集積する大田区で、各分野のスペシャリストとの強固なネットワークをいかし、お客様の製品開発における時間とコストの最適化を実現します。
昭和時代から受け継がれる確かな経験と技術
I-OTAの強みは、昭和時代から大田区で培われてきた確かな技術力と経験値にあります。機械金属加工、精密加工、基盤技術など、多岐にわたる分野で高度な技術を持つ企業が参画しています。
これまでさまざまな産業の製造課題を解決してきた実績があります。特に「仲間まわし」と呼ばれる独自の連携文化により、各社の技術やノウハウを柔軟に組み合わせることで、複雑な製造要件にも対応可能です。伝統的な協力体制を、現代のデジタル技術で効率化し、より迅速で質の高い製造サービスを実現しています。
参画企業との強固な連携体制
I-OTAは単なる製造業の集まりではなく、ハブ企業を中心とした効率的な情報共有と意思決定により、お客様のご要望に迅速に対応します。各参画企業がNDAを締結し、プロジェクト型の共同事業体として機能しているからです。
製造工程の進捗管理や品質管理も一元化されているため、複数の工程を経る製品開発でも、お客様の手間を最小限に抑えることもできます。また、羽田イノベーションシティを活用した定期的な情報交換により、常に最新の製造技術と市場ニーズに対応できる体制を整えています。
ゼロベースから対応できる提案力
図面がない段階からの製品開発にも、I-OTAは豊富な経験でお応えします。お客様のアイデアや構想段階から、市場性や量産化を見据えた具体的な提案が可能です。
製品企画のプロと、各分野の技術者が連携して実現可能性の高い製品開発をサポートでき、試作から量産化まで、一貫した視点でのアドバイスを提供できるためです。I-OTAは伝統的な製造業の強みとデジタル技術を融合させた、新しい時代のワンストップサービスを実現しています。
24時間365日、お問い合わせを受け付けております。製品開発・製造に関するご相談は、まずはお気軽にお問い合わせください。
まとめ
製造業のワンストップサービスは、製品開発における時間とコストの最適化を実現する有効な選択肢です。企画設計から製造、品質管理まで一括して任せられることで、複数業者との煩雑なやり取りから解放され、効率的な製品開発が可能です。
ただし、ワンストップサービスの導入には、信頼できるパートナー選びが欠かせません。そのため、以下のポイントの確認をおすすめします。
- 技術力と設備の実態確認
- 提案内容の具体性
- 連携体制の透明性
まずは自社の製造課題を整理し、ワンストップサービス導入による具体的なメリットを検討してください。その上で自社に最適なパートナーを選定を行うことが成功への近道となります。
I-OTAでは、昭和時代から受け継がれる確かな技術と大田区の優れた製造業ネットワークをいかし、「できること」「できないこと」を明確にお伝えし、プロジェクトの実現可能性を慎重に見極めます。製品開発・製造に関するご相談は、まずはお気軽にお問い合わせください。