金属加工の試作は、品質とコストのバランスを取りながら、確実に要求品質を満たす試作品を作る重要な工程です。単純に作成して終わりではなく、材料選定から加工方法、品質管理まで双方で意見をだしあって進めていく必要があります。
本記事では、金属加工における試作の基本から必要性、加工方法やコストダウンの方法まで詳しく解説します。高品質な試作品を適正なコストで、確実に手に入れたいと本気でお考えの方は、ぜひ最後までご一読ください。
金属加工における「試作」とは
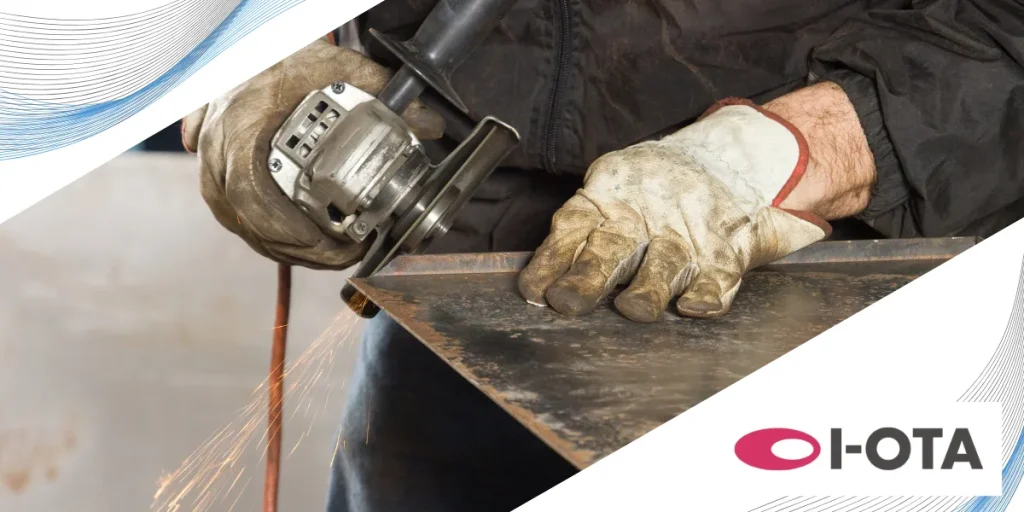
金属加工における「試作」とは、新製品や部品の開発過程で実際の金属材料を使用してサンプルを製作する工程のことです。企画から量産までの開発フローにおいて、設計の妥当性を検証する工程として位置づけられます。
試作の主な目的は、製品の機能や性能、デザインの検証です。実際に形にしてみることで、設計段階では気づかなかった課題や改善点を早期に発見できます。また、量産前に製造工程の検証や品質確認を行うことで、将来的なトラブルも未然に防げます。
試作と生産検証試験(Process verification Test / PVT)の違い
試作は製品設計の検証が主目的であるのに対し、生産検証試験は量産体制の確立を目指す点が大きな違いといえます。あくまでも試作は新製品の設計構想を具現化し、基本的な機能や性能を確認するための初期段階です。
一方で、生産検証試験(PVT)は、量産開始前の最終段階で行われる検証プロセスです。実際の量産と同じ材料・設備・工程を使用して試作品を製作し、以下の3つの観点から検証を行います。
- 製品品質の安定性
- 製造工程の効率性
- 量産時の課題抽出
PVTを通過できれば、量産時の品質基準や製造プロセスが確立され、安定した製品供給の基盤が整うのです。
「試作」と「量産」の違い
項目 | 試作 | 量産 |
---|---|---|
製造数量 | 1個〜数個 | 100個以上 |
重視ポイント | 短納期・フィードバック | 品質安定性・コスト |
製造サイクル | 短期間で複数回の改良 | 確立された工程での継続生産 |
コスト特性 | 単価は高め | スケールメリットで単価低減 |
製造方法 | 切削加工・3Dプリンター等 | プレス・鋳造・金型等 |
設計変更 | 柔軟に対応可能 | 変更コスト大・困難 |
試作と量産のもっとも本質的な違いは、目的にあります。試作は製品の完成度を高めるための検証と改善を重視する一方、量産は確立された仕様に基づく効率的な製造と品質の安定性を追求します。
試作段階では柔軟な設計変更が可能ですが、量産段階での変更はコストと時間を要するため、試作での十分な検証を経ることが重要です。
金属加工で基本となる5つの加工方法
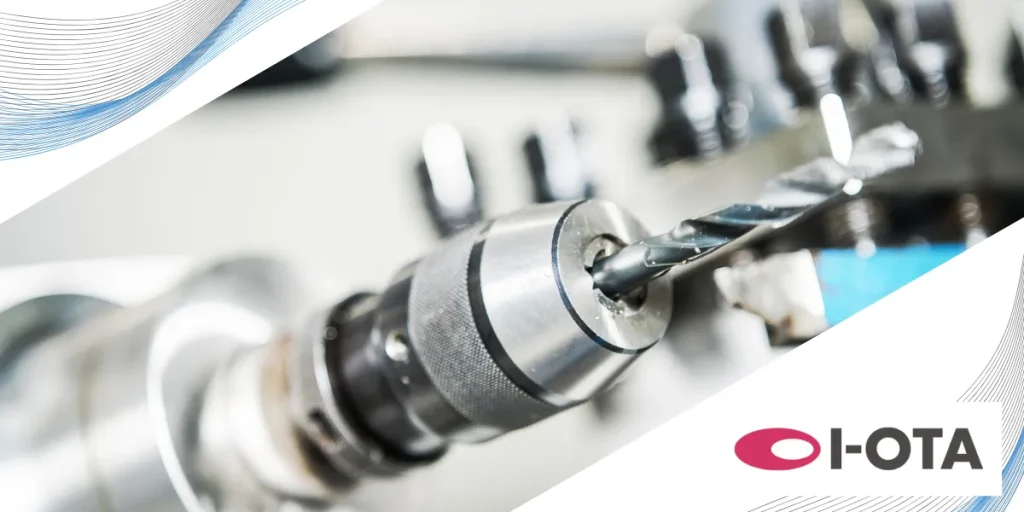
金属加工の基本となる加工方法は、以下の5つに分類されます。
- 切削加工:工具で材料を削り出す方法
- 成形加工:金型を使って形状を作る方法
- 接合加工:複数の部品を組み合わせる方法
- 特殊加工:レーザーや放電などを使う方法
- 熱/表面処理:材料の特性を変える方法
切削加工
切削加工は、旋盤やマシニングセンタなどの工作機械を使用して、金属材料を削り出していく加工方法です。工具で材料を切削し、高精度な寸法精度と優れた表面品質を実現できます。
特に試作段階では、金型投資が不要で1個からの製作が可能なため、もっとも一般的に選ばれる加工方法です。複雑な3次元形状も加工できることから、機械部品や精密機器の試作に適しています。
成形加工
成形加工は、プレス加工や鋳造、鍛造などで金型を使用して材料に圧力をかけ、目的の形状に成形する加工方法金型製作に初期投資が必要ですが、一度金型ができれば短時間で同じ形状の製品を大量生産できます。
試作段階では、量産時の品質や生産性を検証するために、実際の量産と同じ金型を使用して少量の製品を作ることがあります。
接合加工
接合加工は、複数の部品を溶接、ろう付け、接着などの方法で結合する加工方法です。一体成形が困難な複雑な形状や、異なる材料を組み合わせる場合に使用されます。
試作品の製作では、設計変更の柔軟性が高く、部品ごとに最適な加工方法を選択できる利点があります。また、量産時の組立性や接合強度の検証にも一役買う加工方法です。
特殊加工
特殊加工は、レーザー加工や放電加工、電子ビーム加工など、従来の機械的な加工方法では対応が難しい加工を可能にする方法です。超硬材料の加工や微細加工、複雑な形状の加工に適しています。
試作といった新しい製品開発や技術革新において役割を果たし、従来の加工方法では実現できなかった形状や機能の実現を可能にします。
熱/表面処理
熱処理や表面処理は、材料の特性を改善したり、製品の耐久性を向上させたりする加工方法です。
熱処理では、焼入れや焼戻しにより材料の硬度や強度を調整し、表面処理では、メッキや陽極酸化などにより耐食性や意匠性を向上させます。試作段階でこの処理を行うことで、量産時の品質や性能を事前に確認できます。
このように、金属加工にはさまざまな方法がありますが、なぜ試作が必要なのでしょうか?ただプロセスに組み込まれているから『やらなくてはならない』というものではありません。
失敗しないためにも、金属加工において試作が求められる理由について再確認しましょう。
金属加工で試作の必要性が高い3つの理由
金属加工で試作の必要性が高い理由には、以下の3つが挙げられます。
- 量産前に製品を評価するため
- 量産加工に必要な検証を行うため
- 仕様変更を減らすため
量産前に製品を評価するため
金属加工において、量産前の製品評価は極めて重要な工程です。試作品を通じて、以下のようなあらゆる側面で評価を怠ると、量産後に重大な問題を引き起こすリスクが高まるからです。
- 品質
- 機能
- デザイン
- 形状
- コスト
例えば、実際の使用環境での強度不足や、組み立て時の干渉といった問題は、図面や3Dデータ上では気づきにくい課題です。試作品があれば早期に問題を発見し、設計変更や材質変更などの対策を講じることができます。
また、製品評価の段階で見つかった改善点は、比較的低コストで修正も可能です。量産後の手直しと比べると、時間的にも費用的にも優位性があります。
量産加工に必要な検証を行うため
試作段階で製品に問題がないか、改良の余地はないかなどを徹底的に確認できれば、量産時のリスクを最小限に抑えられるのも1つの理由です。検証を省略して直接量産に移行した場合、製造ラインの停止や大量の不良品発生といった深刻な問題に発展しかねません。
金属加工の検証では、加工精度や表面処理の品質、組立性など、実際の製造工程で起こり得るさまざまな課題を事前に把握できます。結果、量産時の品質安定化とコスト最適化を同時に実現できるのです。
仕様変更を減らすため
金属加工において、量産開始後の仕様変更は莫大なコストと時間のロスを招きます。特に金型を使う場合、1つの変更で数百万円単位の追加費用となることも珍しくありません。
こうしたケースでも試作を通じて、設計上の問題点や改善点を洗い出し、修正を加えることで量産後の予期せぬ仕様変更リスクを低減できます。また、製品の機能や性能要件を満たしているかの確認も、この段階で確実に行えます。
このように、試作は製品開発における投資であり、ただ取り決められたプロセスではないといえます。
では、実際の試作にはどの程度の費用が必要なのでしょうか?次は、金属加工の試作にかかる具体的な費用の目安を見ていきましょう。
金属加工の試作にかかる費用
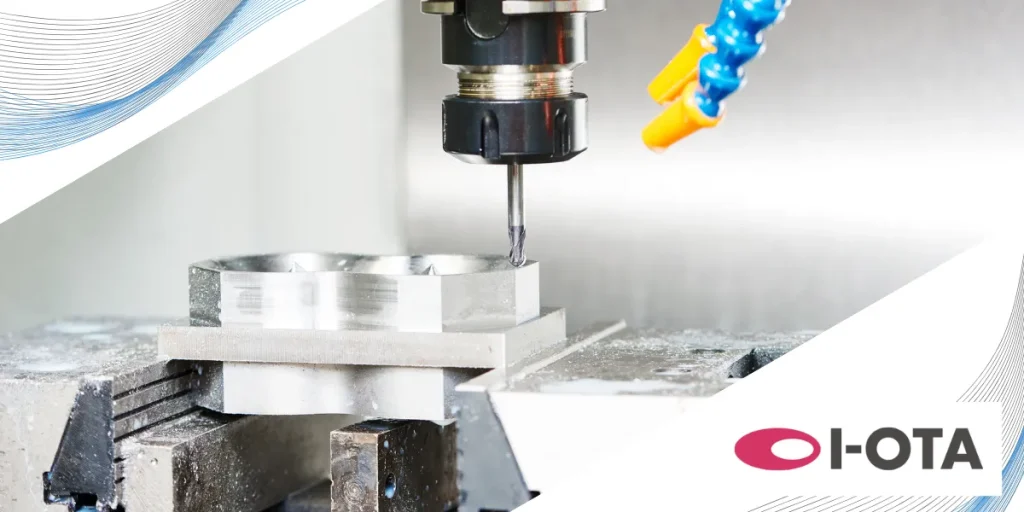
金属加工の試作費用は、一般的に数十万円から数百万円程度が相場となります。試作するモノは大小さまざまで、実際の費用は案件ごとに変動します。
試作にかかる主な費用の内訳は、以下のとおりです。
- 材料費(金属素材の調達費用)
- 加工費(切削、成形などの工程にかかる費用)
- 人件費(技術者の作業工数)
- 設備費(工作機械の使用料)
- 検査費(品質確認にかかる費用)
- 管理費(工程管理などの間接費用)
特に費用を左右する要因としては、試作品の大きさ、形状の複雑さ、要求される精度、材料の種類が挙げられます。加えて、複雑な形状や高い精度が求められる場合は、加工時間が長くなり工程も増えるため、費用も上昇すると考えましょう。
また、金属加工の試作にかかる費用は、発注数量(ロット数)によっても変わってきます。では、具体的にロット数がどのように試作費用に影響するのか、次で詳しく見ていきましょう。
金属加工の試作費用とロット数の密接な関係
金属加工の試作費用はロット数(製作個数)によって変動し、少量試作では1個あたりの単価が高くなる傾向にあります。たった1つの試作であっても単価が高くなるのには、3つの理由があります。
- 試作品でも規定の単位で材料を購入し、余剰分のコストが単価に影響するから
- 加工機の段取りや調整にかかる工数は100個作る場合でもほぼ変わらないから
- 試作品は要求精度が高く、1個1個の入念な検査が必要となるから
ただし、一例であり、製品の複雑さや要求精度、依頼先の工場の体制や設備によって変動します。とはいえ、試作費用は決して安価ではありません。
どのような理由であっても、予算には限りがあるのもまた事実です。次は、試作費用を抑えるための具体的な方法を紹介します。
金属加工の試作をコストダウンする3つの方法
金属加工の試作をコストダウンする方法は、以下の3つです。
- 納期に余裕を持つ
- 材料や数量を見直す
- 一貫生産で依頼する
納期に余裕を持つ
短納期での試作依頼は、一見すると開発スピードを上げられるように思えます。しかし、急いで作った試作品に不具合が見つかり、再度試作をやり直すケースが少なくありません。
結果、時間もコストも二重にかかってしまいます。むしろ、最初から適切な納期を設定し、十分な品質確認の時間を確保するほうが依頼先での工夫やテストも十分に行えて、トータルでのコストダウンにつながります。
また、製作を依頼する際は、加工業者の技術者と綿密な打ち合わせを行い、要求品質を満たすために必要な工程や時間を明確にしておくことも重要です。社内での工程管理も円滑になり、手戻りのリスクを最小限に抑えられます。
材料や数量を見直す
試作段階では、最終製品と全く同じ材料や仕様にこだわる必要はありません。むしろ、評価目的に応じて材料を変更したり、必要最小限の数量に絞ったりする工夫によって、コストダウンできることもあります。
例えば、強度評価が目的であれば、表面処理を省略した状態での試作も検討できるケースがあります。また、従来使用していた材料でも、新しい加工方法を採用し、より効率化できることもあるでしょう。
固定観念にとらわれず、目的に応じた柔軟な材料選定や数量設定を行うことが、コストダウンのポイントです。
一貫生産で依頼する
複数の加工工程を異なる業者に依頼すると、それぞれの段階で調整や運送のコストが発生します。これに対し、I-OTAのような一貫生産体制を持つ企業に依頼できれば、工程間の無駄を省き、トータルでのコストダウンが可能です。
I-OTAでは、切削加工から表面処理まで、すべての工程を一元管理しています。小ロットの試作でも、効率的な製造プロセスを構築しているため、競争力のある価格を実現しています。
高品質な試作品の製作とコストダウンの両立にお悩みでしたら、ぜひI-OTAにご相談ください。経験豊富な技術者が、お客様のニーズに最適なソリューションをご提案いたします。
金属加工の試作におけるたった1つの注意点
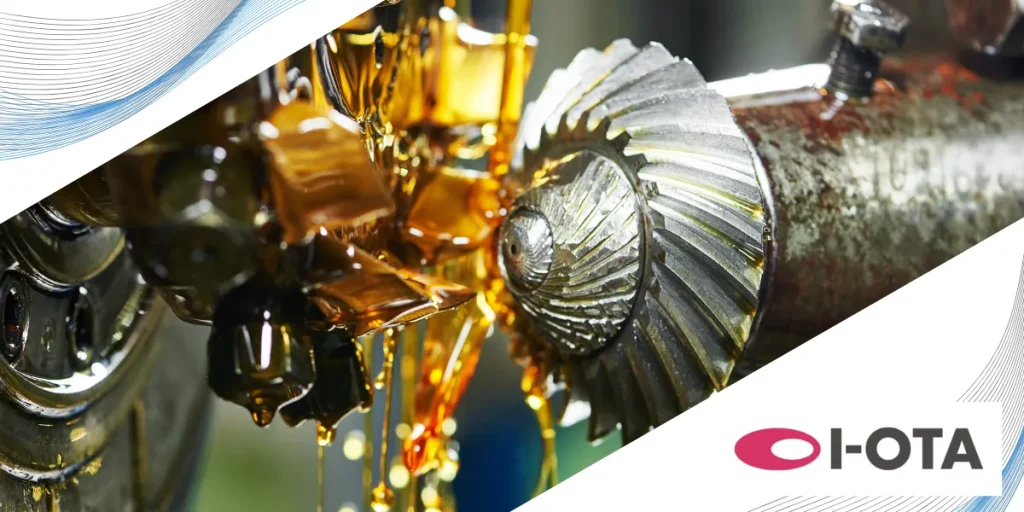
金属加工の試作において、もっとも注意すべき点は「安さだけを追求しない」ことです。試作段階でのコスト削減は一見賢明に思えますが、それが製品化後のリスクとなる可能性も捨てきれません。
よくあるのは、安価な試作を選ぶことで製品の強度や耐久性が十分に検証されないまま量産に移行してしまうケースです。製品の不具合や品質問題につながり、最終的には製品の手直しや市場からの回収など、予期せぬ高額なコストが発生する原因となります。
「なぜ試作にそこまでコストをかける必要があるのか」と疑問に思われるかもしれません。
しかし、適切な試作への投資は、将来的な収益性や市場での競争力を高めるための布石ともなります。品質の高い試作を通じて製品の完成度を高め、競合と差別化しつつ付加価値による高価格帯を狙うといった戦略もまた一案だからです。
もちろん、予算や市場環境との兼ね合いは重要です。しかし、『とにかく安く作る』という発想から一歩踏み出し、『少しの投資で得られる価値』にも目を向けることが、新たなビジネスチャンスを掴むこともある、ということを覚えておきましょう。
金属加工の試作を作る際の流れ
金属加工の試作を作る際の流れは、以下のとおりです。わかりやすくするため、I-OTAを例に紹介します。
- 初回相談・ヒアリング
- 見積り提示
- 発注・契約
- 製造工程の確定
- 試作品製造
- 完成・納品
特に大切なのは、初回相談時のヒアリングです。加工精度や表面処理の要件、測定箇所など、細かい要求事項があれば、この段階でお伝えいただくことで、手戻りのない円滑な試作が可能になります。
また、試作後の量産を視野に入れている場合も、初期段階でお知らせいただけると、量産時のコストダウンを考慮した試作方法をご提案できます。
金属加工の試作はI-OTAにお任せください
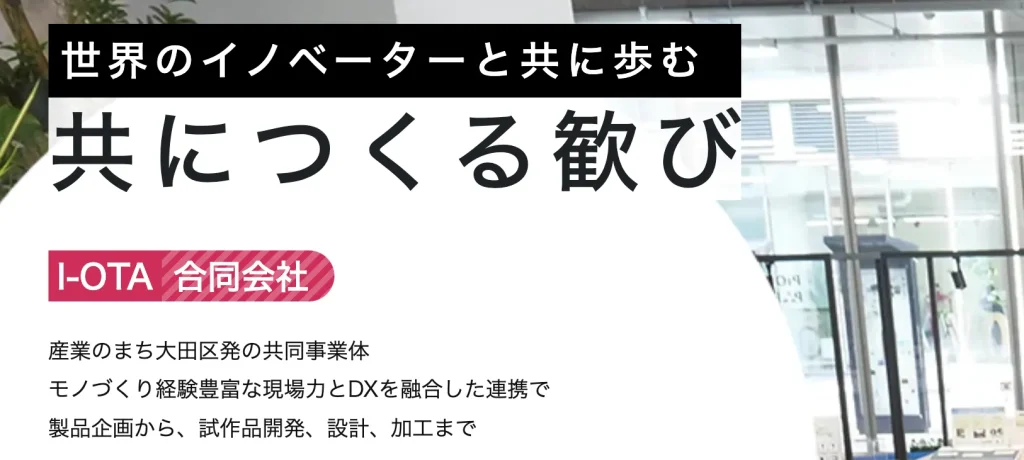
金属加工の試作において、品質とスピード、そしてコストの最適なバランスを実現するパートナーをお探しではありませんか?I-OTAは、大田区を拠点とする日本トップクラスの技術力を持つ製造業の共同事業体として、お客様の試作ニーズにお応えします。
図面をお持ちの方はもちろん、アイデア段階からの相談にも対応し、製品企画から試作開発、設計、加工まで一貫したサポートを提供しています。特に金属加工の分野では、長年の実績と経験を活かし、単なる製造だけでなく、コスト削減や量産化を見据えた改善提案まで行うことが可能です。
以下の3つの特徴から、なぜI-OTAが最適な試作のパートナーとなるのかをご説明します。
共同事業体でワンストップ
I-OTAの強みは、金属加工のスペシャリストが集結した共同事業体としての一貫生産体制です。切削加工、成形加工、接合加工、特殊加工、表面処理まで、あらゆる加工技術に対応可能な企業がネットワークでつながっています。
「ここはA社で、ここはB社に依頼して…」という面倒な連携に工数を割く必要はありません。複数の加工工程が必要な試作品でも、お客様は1社に依頼するだけで完成品までたどり着けます。
1個から小ロットにも対応
試作段階では、必要最小限の数量から始めたいというニーズにも柔軟に対応します。I-OTAでは、1個からの試作製作を受け付けており、お客様の開発フェーズに合わせた最適なロット数での製造が可能です。
少量生産でありながらも、量産時と同等の品質を確保し、製品評価や機能検証に必要な精度を実現します。また、試作から量産への移行を見据えた段階的なスケールアップにも対応可能で、スムーズな量産化を実現します。
技術者の目線からのご提案
I-OTAの技術者たちは、単なる製造請負ではなく、お客様のプロジェクトの成功をともに目指すパートナーとして、技術的な観点から積極的な提案を行います。
長年の製造経験を活かし、設計段階からコストダウンの可能性や製造効率の改善点を見出し、具体的な解決策を提示できるからです。また、最新の加工技術や材料知識を活用し、より優れた製品実現のための改善提案も行います。
I-OTAは、ワンストップの一貫生産体制と確かな技術力で、お客様の製品開発をトータルでサポートします。まずは、お気軽にご相談ください。
まとめ
金属加工の試作は、品質とコストのバランスを取りながら、確実に要求品質を満たす試作品を作るための重要な工程です。目的は、量産前の製品評価、製造工程の検証、そして仕様変更リスクの低減にあります。
試作費用は、材料費、加工費、人件費などで構成され、ロット数によって変動します。ただし、単なる価格の安さだけを追求するのではなく、品質と将来的なリスク低減のバランスを考えることも重要です。
I-OTAは、共同事業体としての総合力、1個からの柔軟な対応、技術者視点からの提案力を強みとしています。高品質な試作品の実現に向けて、まずはお気軽にご相談ください。
確かな技術力と豊富な経験を持つI-OTAが、お客様の製品開発の成功をサポートいたします。
よくある質問(FAQ)
金属加工は1個から依頼できる?
はい、I-OTAでは1個からの試作品製作に対応しています。試作段階では、少量生産からスタートしたいというニーズが一般的です。弊社では、そうしたお客様のご要望にお応えするため、最小ロット1個からの受注体制を整えています。
ステンレス加工の依頼はできる?
はい、I-OTAではステンレス加工もご依頼いただけます。SUS304やSUS316Lなど、一般的なステンレス材から特殊なステンレス材まで、幅広い材質に対応可能です。
チタン加工の依頼はできる?
はい、I-OTAではチタン加工にも対応しています。純チタンからチタン合金まで、さまざまな材質での加工実績があります。特に医療機器や航空宇宙関連部品など、高い信頼性が要求される分野での豊富な実績があります。